With the increasing trend towards more sophisticated packaging and industrial materials, laminated and composite flexible structures are being widely used for many applications. By combining the unique barrier, sealability and structural properties of several different substrates, a composite laminate is realized with the characteristics required for specialized packaging and industrial applications. Extrusion coating is one of the processes used to produce a large range of thin multilayer structures.
.
Introduction
Extrusion coating is one of the processes used to produce a large range of thin multilayer structures. In the extrusion coating of polyethylene, a molten web of extruded polymer is applied as a thin coating onto a substrate which is passing continuously through a nip-roll assembly. In extrusion lamination, the molten polymer is applied as an adhesive layer between two substrates to form a laminated structure. The substrate may be paper, paper board, polyester film, polypropylene film, aluminum foil, woven fabric, etc.
The polyethylene coating provides increased tear resistance, scuff resistance, a heat sealable surface, resistance against chemicals, grease resistance, and a good barrier against water and various gases.
.
Low density polyethylene (LDPE) grades are characterized mainly by their melt flow index (MFI) and density. The way in which these parameters affect the physical and chemical properties of the polyethylene are shown in the figure below.
(Melt Flow Index (MFI) is the melt flow of polymer extrudate in g/10 min when subjected to a load of 2.16 kg).
.
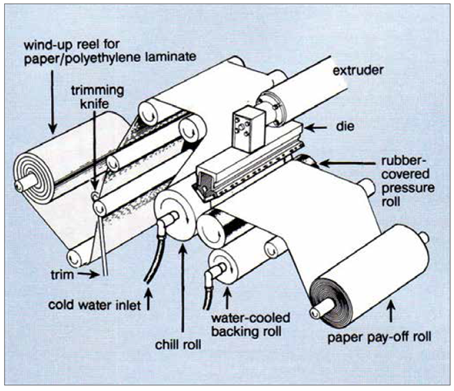
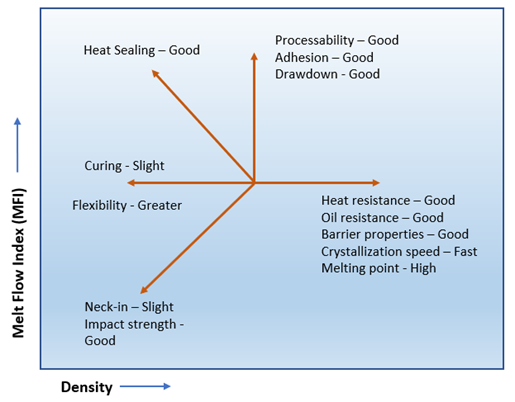
Extrusion Coating Process
In the extrusion coating process, polyethylene is melted under heat and pressure in an extruder and the molten polymer is extruded through a slit die as a thin web. This web, at high temperature, is drawn down and coated onto a flexible substrate in a nip-roll assembly formed by a water-cooled chill roll and a rubber-covered pressure roll. The substrate to be coated is fed continuously from an unwind reel over the rubber pressure roll into the nip where the laminate is formed by pressing the two layers together. The laminate is rapidly cooled by the chill roll and is taken up by a wind-up mechanism.
For extrusion coating, a single screw extruder is generally preferred with a screw length to diameter ratio of greater than 25:1 to ensure proper mixing. Good mixing of the melted polyethylene is essential if a good coating film with no defects or blemishes is to be obtained. Defects which may be apparent as a result of a non-homogeneous melt include:
.
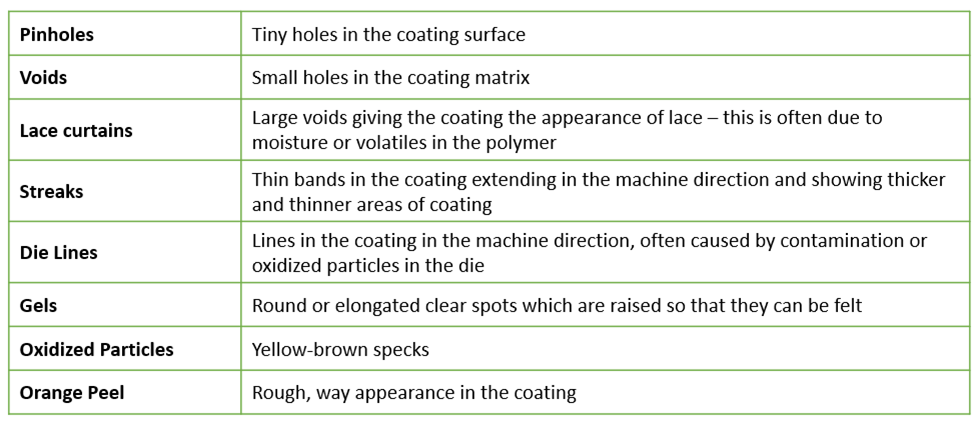
.
The Die: The prime objective in an extrusion coating slit die is to have the melt leaving the die at constant velocity across the full width.
The Air Gap: In the air gap, some of the properties of the laminate are most affected by extrusion conditions. It is here that the molten web is drawn down and necks-in (see pg. 8) and oxidation takes place. A large gap may cause premature cooling of the melt, increasing its viscosity which in turn may lead to poor adhesion to the substrate. However, if the air gap is too small then this can also result in a deterioration of adhesion strength.
Nip Assembly and Chill Roll: It is designed to remove the maximum amount of heat from the polyethylene. The temperature of the chill roll should be kept at approximately 15 to 30°C; if it increases to 55 to 60°C or higher, the polyethylene may stick to the chill roll, causing partial delamination between the coated web and the substrate, or even web breakage.
Edge Trimming: It is not possible to coat the molten web to the same width as the substrate, due to two different effects which modify the edges of the web. One of these effects is known as edge weave. The other is the thickening at the edges of the web to form an edge-bead. This is a consequence of the necking-in of the web between the die and the nip. To overcome these faults, it is necessary to remove edge trim (consisting of polyethylene and/or substrate) continuously by means of slitting knives.
Reeling and Windup equipment: Since the coating line must run continuously, flying splice unwinds and rewinds are usually installed to permit automatic reel changes at full production speed.
.
Effect of Processing Conditions on Laminate Properties:
Melt Temperature
The melt temperature used varies according to the substrate being coated, customer requirements regarding desired properties, and the equipment. Temperatures can be between 265oC and 330°C but 300 to 320°C are typical.
Properties such as gloss and clarity improve with increasing operating temperatures. However, if the temperature is too high, the melt exiting the die may be too fluid for coating. It may also be difficult to cool and wind up, and excessive oxidation may occur. Oxidation is a prerequisite for good adhesion but can lead to inferior heat sealing and the possibility of odor and taint problems.
Low melt temperatures on the other hand may give the polyethylene coating better frictional properties and allow heat sealing at greater speeds (shorter dwell time) and at slightly lower temperatures. This may be at the expense of adhesion.
.
Coating Weight, Neck-in and Drawdown
Coating weights range from as low as 8 to 10 g/m2 for packaging films and up to 50 to 100 g/m2 for certain heavy-duty cartons and fabric coatings. Associated with coating weight are two important properties of the extruded web, “neck-in” and “drawdown”.
Neck-in is the reduction in width of the molten film web which occurs as it leaves the die. It is measured as half the difference between the width of the coating at the nip and the width of the die. Neck-in is caused by surface tension and melt elastic effects in the immediate vicinity of the die exit.
.
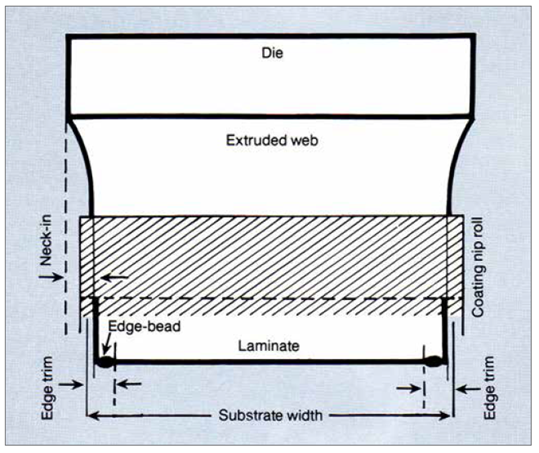
.
Drawdown refers to the ability of the polymer to coat evenly down to very low coating weights without breakage. It involves the reduction in thickness of the molten polyethylene after leaving the die and before contacting the substrate. It is a limiting factor in the maximum line speed obtainable.
Neck-in and drawdown are a function of MFI and melt temperature. The maximum line speed (drawdown) increases with increasing MFI, but neck-in performance gets worse. The choice of a coating polymer is thus a compromise between drawdown and neck-in performance. Most extrusion coating polyethylene has an MFI in the range 4 to 12 g/10 min.
.
Other factors playing a role in determining neck-in performance and maximum drawdown:
- Line speed. Neck-in values decrease with increasing line speed.
- Processing temperature. Neck-in increases & drawdown improves with increasing temperature.
- Air Gap. Large air gaps give better drawdown but worse neck-in.
- Polymer swelling ratio. (Defined as the initial thickness of the polymer melt exiting the die over the die gap). Neck-in decreases but drawdown is worse as the swelling ratio increases.
.
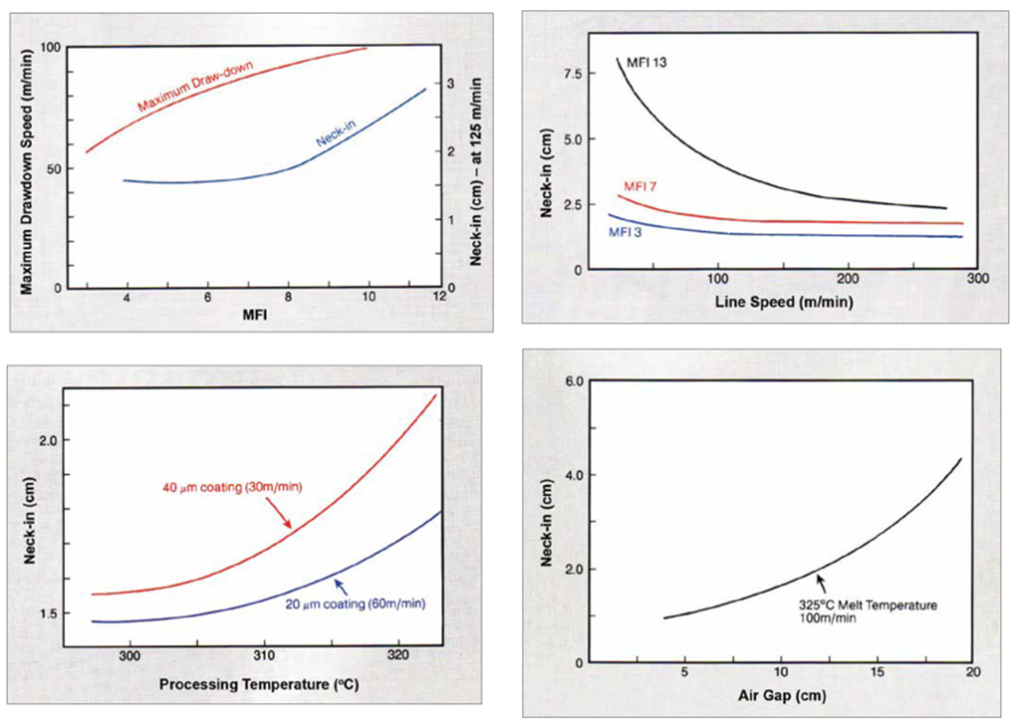
.
Extrusion Coating Troubleshooting Guide:
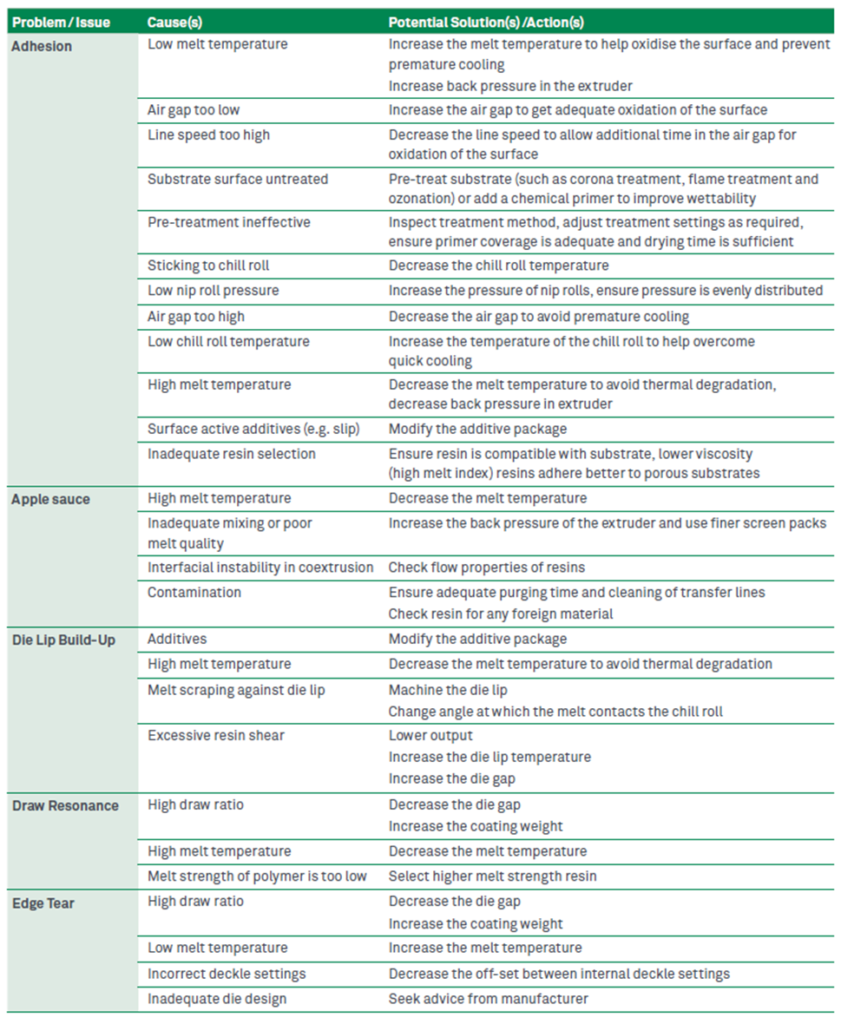
.
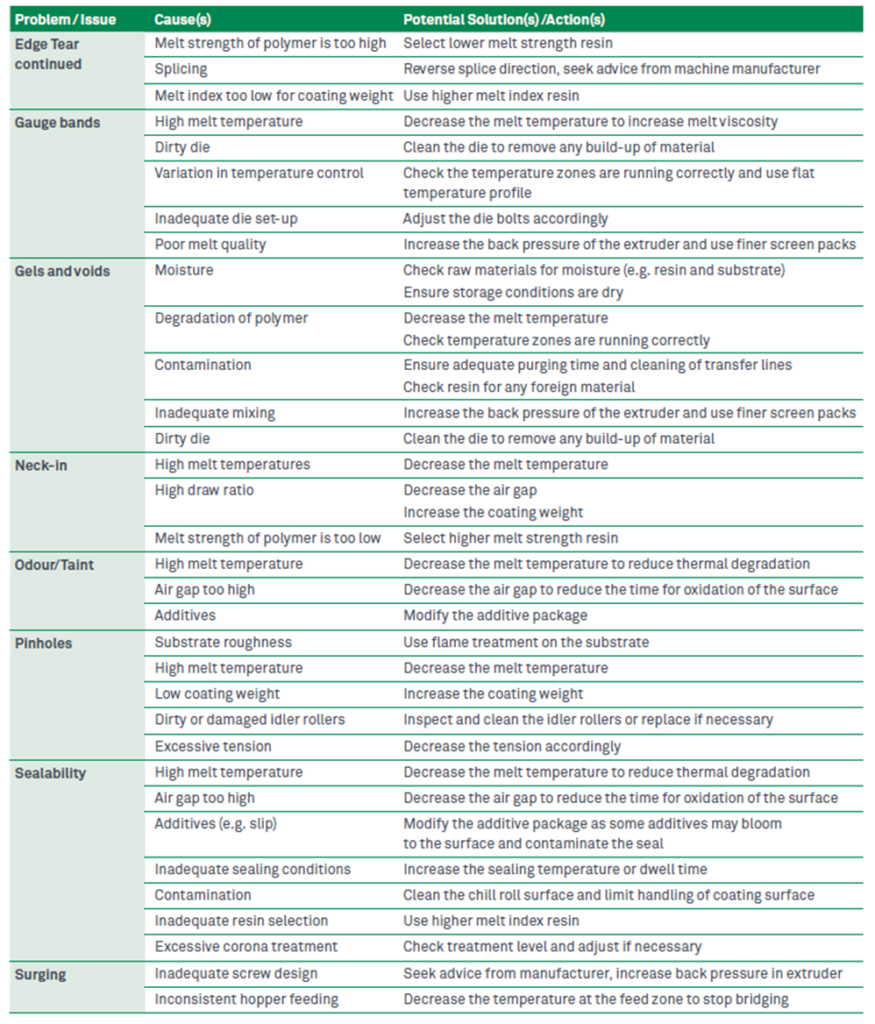
.
Properties of Extrusion coated Laminates:
Frictional Properties
One of the important final properties of the coated laminate is the ease with which it will slide or slip over another surface, i.e., its coefficient of friction (COF). A similar property is blocking, which is the tendency of adjacent surfaces in intimate contact to stick to each other, making separation difficult.
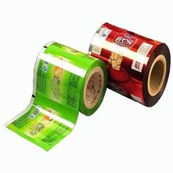
The COF and blocking of the coated polyethylene surface are affected by such factors as coating temperature, chill roll temperature, chill roll surface finish, overtreatment during corona discharge treatment, and of course, the presence or absence of slip and antiblocking additives in the polyethylene.
.
The COF decreases as polymer density increases. It is unaffected by the air gap distance but may decrease slightly at low melt temperatures. A high coating temperature and a highly polished chill roll can contribute to blocking. Increased chill roll temperature will increase slip & decrease blocking.
.
Heat Sealing
Polymer density, MFI, and film thickness affect the “sealability” and the strength of the heat seal bond. Density controls the minimum temperature at which sealing takes place and the amount of heat required to melt the polymer.

The strength of the seal while still hot is important particularly with high speed automatic filling and packaging machines, where the product is introduced into the package almost immediately after the seal has been formed. For instance, many paper board laminate seals are under tension, with the tendency to reopen when the sealing pressure is released. Sufficient melt strength is required to ensure that the seal remains intact until it cools. The hot tack strength is one measure of a polymer’s performance in situations such as this. A strong bond over as wide a temperature range as possible is indicative of good performance.
.
Barrier Properties
An important function of any laminate is to provide a barrier against a variety of gases, vapors or liquids. Polyethylene generally provides a good to excellent barrier to such materials and the performance will usually improve as the density increases and the MFI decreases. Improved barrier properties are also achieved as the coating weight is increased.
.
Food Contact – Odor and Taint
Odor and taint are often caused by additives in the polymer or by excessive oxidation of the polymer at the high temperatures used for extrusion coating. There is no apparent relationship between odor or taint of the coating and parameters such as density and MFI.
..
.
References
- Chapter 04: Extrusion Coating & Lamination. Quenos.
- Bezigian, T.; Extrusion Coating Manual (4th Ed.), TAPPI Press, 1999.
- Gregory, B. H.; Extrusion Coating: A Process Manual, Trafford Publishing, 2007.
- Rolando, T. E.; Flexible Packaging – Adhesives, Coatings and Processes, Volume 11, iSmithers Rapra Publishing, 2000.
- Kouda, S.; Prediction of Processability at Extrusion Coating for Low-Density Polyethylenes, J. Polym Eng Sci, 48, 1094, 2008.
- Sollogoub, C.; Montmitonnet, P.; Demay, Y.; Agassant, J. F.; Deparis, P.; Origin of the Bubble Defect in the Extrusion Coating Process, J. Polym Eng Sci, 51, 347, 2011.
- Hammond, F. M.; Hansen M. H.; Improving aluminum adhesion and heat seal performance of LDPE and LLDPE extrusion coating resins, Tappi J., 74, 232, 1991.
- Wagner, J. R. Jr; Handbook of Troubleshooting Plastic Processes: A Practical Guide, John Wiley and Sons, 2012.
- Frey, K. R.; Optimising Time in the Air Gap in Extrusion Coating for Improved Adhesion, TAPPI Place Conference, 2012.
- Ferrari, D.; Extrusion Coating Resins – Troubleshooting, TAPPI PLC Conference, 2000.