In this Tech-File, we will be discussing primarily about the roll coating application technique. Roll coating is one of the many types of coating techniques (few coating techniques to name: spray coating, powder coating, screen coating, curtain coating, knife coating, transfer coating, and dip coating). Roll coating itself consists of subcategories which we will be discussing in this literature.
Roll coating is widely used in printing and packaging industry for applying coatings and adhesives. Knowing about the different components of roll coating and its working mechanism will give coating and adhesive formulators a better understanding for developing their products as per application technique.
.
Roll coating is and efficient method applicable only to uniform flat or cylindrical surfaces. Relatively slow evaporating solvents must be used to avoid viscosity buildup on the rolls of the coater.
..
.
Kiss Roll Coating
This is the simplest kind of roll coating. In this setup a single rotating roller acts as both a metering device and an application device. Half of the roller is immersed in the coating bath, and as it rotates, it carries a film on its surface which is then transferred on the substrate as the roller rotates. The coating thickness is optimized by hydrodynamics, by varying the rotating speed of the roller, coating viscosity and surface tension.
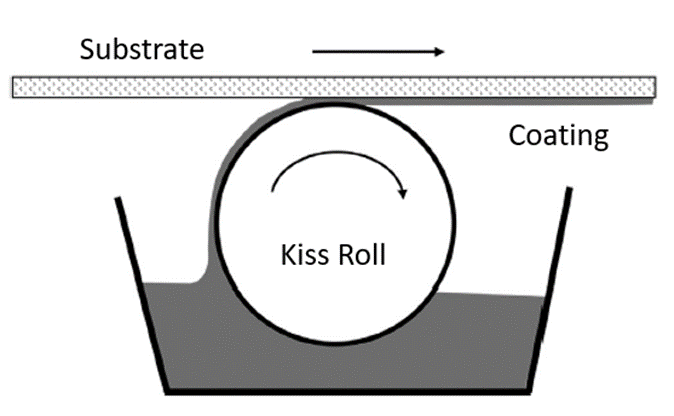
.
Direct Roll Coating
In direct roll coating, the substrate passes between two rollers – the applicator roller and a backup roller, which are rotated in opposite directions. The rollers pull the material being coated between them as shown in figure below. Direct roll coating is used for coating sheets and coils.
.
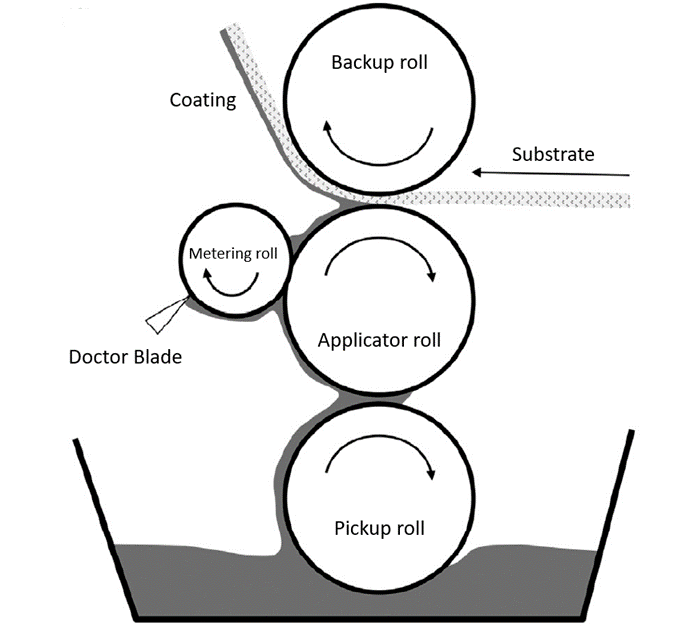
.
The pickup roll runs partially immersed in a tray, containing the coating. It transfers the coating to the applicator roll rotating in the same direction. A simultaneous metering roll rotates in the opposite direction of the applicator roll. The metering roll helps to maintain the coating thickness with the help of a doctor blade, by optimizing the clearance between the blade and the roll.
Such type of an arrangement can be used for high viscosity coatings.
Failure to clean the metering roller surface will result in coating defects, such as streaks or film roughness.
.
Reverse Roll Coating
In reverse roll coating, both the rollers (application roller and support roller) rotate in the same direction, with the substrate being pulled between the two rolls. This process is widely used for coating coils and is not much feasible for sheets.
Reverse roll coating has the advantage that the coating is applied by wiping rather than by film splitting. A smoother film is formed, and the problems of leveling are minimized.
It is the flow in the metered gap, which is the crux of all reverse roll coaters, determining the coating thickness and uniformity.

..
Gravure Roll Coating
Gravure roll coating is the process where engraving on the roller acts as a metering device. The engraved roller is partly submerged in the coating bath and as it rotates, coating liquid fills the engraved pattern and excess coating liquid forms a film on the roller’s surface. A doctor blade removes the excess surface film from the gravure roller surface, and it then presses against the substrate to transfer the coating material in the engraved pattern to the substrate.
Gravure roll coating is a technique that has evolved from the printing industry and used to apply very thin coatings of low viscosity liquids at high speed.
Gravure rolls are characterized by the number of cells per unit area of the roll surface.
.
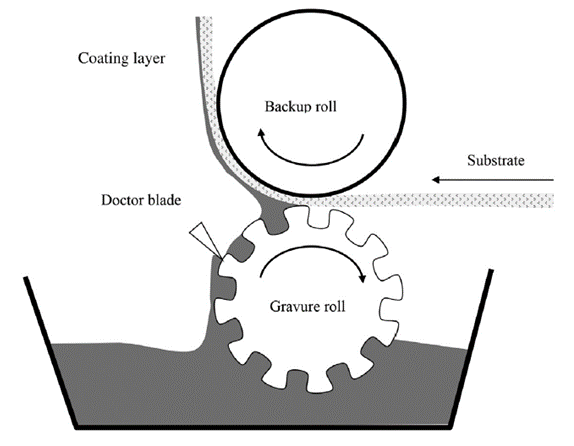
.
Direct gravure coating: In direct gravure coating the moving web is held against the roll by either a backing roll or by applying a high tension and wrap angle to the web. The web moves in the opposite direction to the surface of the roll at roughly the same speed.
Offset gravure coating: An offset gravure system makes use of two rolls: a gravure roll and rigid roll covered with a thick layer of a deformable material (rubber). These are nipped together such that the gravure roll is impressed into the adjacent deformable roll surface, producing what is referred to as a negative gap. Both the rolls rotate in the same direction but at a different speed which controls the coating thickness. Offset printing results in a clear and sharper image.
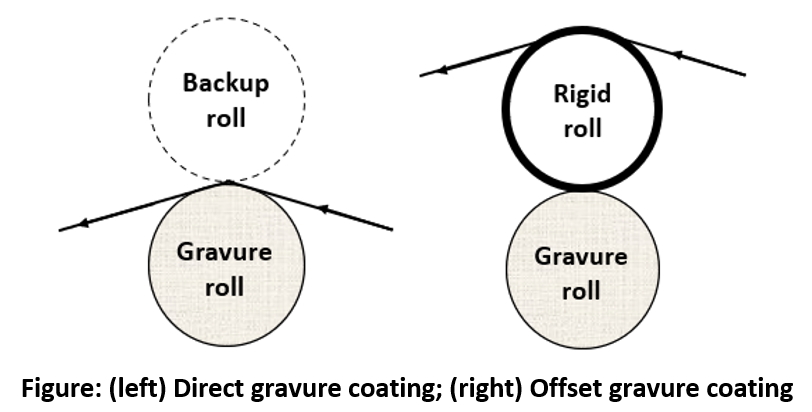
.
.
References
- Organic Coatings – Science and Technology. 3rd Edition. Wiley 2007.
- Smart Textile Coating and Laminates. 2nd Edition. Coating and laminating processes and techniques for textiles. E. Shim. North Carolina State University, Raleigh, NC, United States. 2019.
- Permeability properties of Plastics and Elastomers. 4th Edition. Production of films, containers, and membranes. Lawrence Mckeen. 2017.