Dispersion is the process where a non-soluble solid is suspended in a liquid and stabilized against settling, separation, agglomeration, or aggregation. The concentration of solids in the liquid must be uniform during mixing. Once mixing is removed, the mixture must be stable. For paints and coatings, pigments are being dispersed into a resin/solvent matrix, and stability against settling, flooding, floating or flocculation is required.
.
Properties of the coating such as viscosity, tint strength, opacity, dispersant demand, and photo stability all depend on the particle size of the pigment.
.
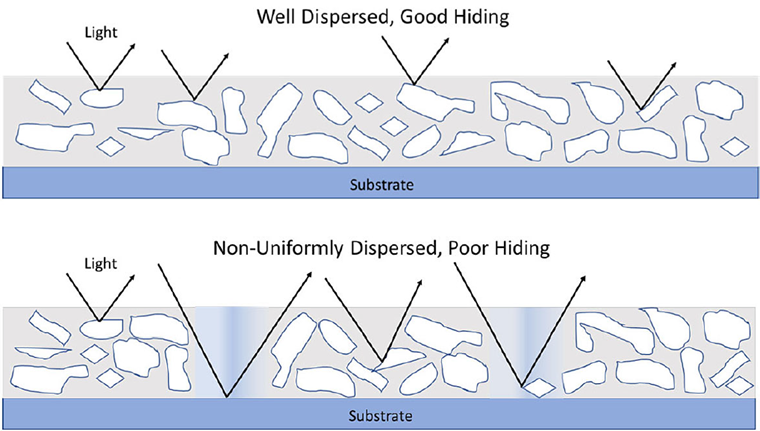
.
.
What is a Dispersant? How does it work?
All Dispersing Agents have two parts: i) Anchoring group and ii) Soluble tail.
First, anchoring groups adsorb to the pigments and fillers surface. They form strong physical bonds with chemical groups that are present on the surface of the particles, the so-called anchor sites.
Second, soluble tails create a layer around the solid particles preventing dispersed particles to glue together again and ensuring colloidal stability.
.
Why is the Dispersant offering so wide and varied?
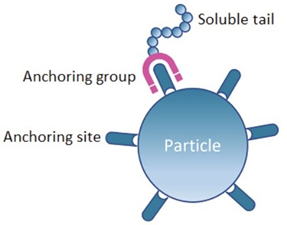
If there is no affinity between the anchor groups of the dispersant and the anchor site of the solid particles, bonding fails, and the dispersant can’t play its role in the formulation.
Chemicals functional groups (anchor sites) at the surface of pigments and fillers vary a lot. Some are surface-treated, and others are not. So that proper anchoring can take place, dispersing agents also come with a great variety of functional groups. To name a few, you will find grades with amine, amide, sulfonate, or phosphate anchoring groups.
On the other hand, the dispersant tail must be soluble in the paint medium and compatible with the binder. Again, depending on the binder and solvent characteristics, formulators need different solutions.
This is the reason why the dispersant offering is so wide.
.
Selecting the right Dispersant
Dispersing agents are typically used to solve issues of pigment settling, flooding, floating, and pigment flocculation. But there are many criteria which must be studied and understood before selecting a dispersant for your system.
- For solvent-based systems, electrostatic stabilization is impossible; steric stabilization is the only way. For water-based systems, electrostatic and steric stabilization both can prove to be useful. Some modern dispersants also offer electro-steric stabilization in a single molecule.
2. As your dispersant molecules need to bond with the solid particle, it is important to identify the anchoring opportunities you have with your pigments and fillers.
3. The non-adsorbing moieties of the dispersing agent should demonstrate excellent compatibility with the binder system. This is essential for optimal stability in the liquid phase as well as best film performance.
4. Understand the chemistry of different dispersants before making the selection.
.
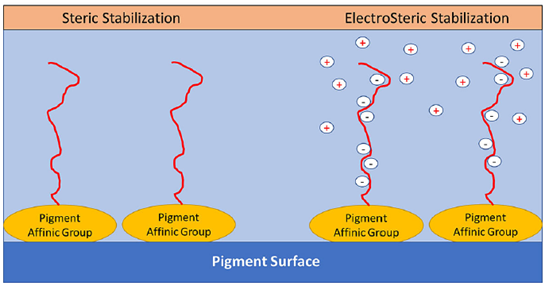
.
Chemistries behind Dispersing Agents
1. Conventional Dispersing Agents
These are mainly low molecular weight and are based on polyesters, polyamides, polyglycols and fatty acid chemistry (FAME).
General Characteristics:
- Mol wt. = 500 – 2000 g/mol
- Good compatibility with the media
- Provide mainly electrostatic stabilization.
.
2. Polymeric Dispersing Agents
These are mainly polyacrylates, polyester, polyether, or polyurethane-based systems.
General Characteristics:
- Mol wt. = 5000 – 50,000 g/mol
- Very effective for long term stabilization
- Provide mainly steric stabilization.
- Provide multiple pigment anchoring groups.
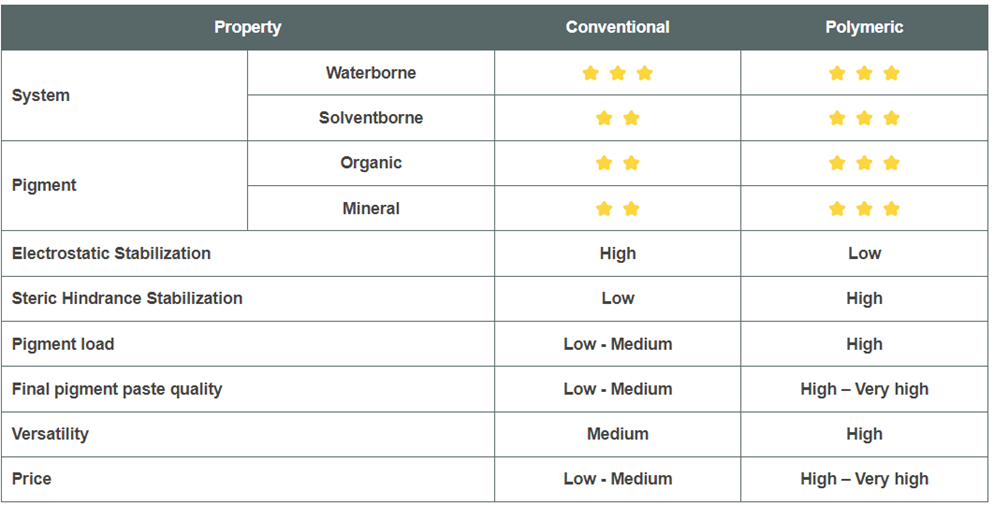
3. Ionic and Non-ionic Dispersing Agents
These are mainly alkyl phenol ethoxylate and more precisely nonyl phenol ethoxylate
General Characteristics:
- Mol wt. = 300 – 1,000 g/mol
- Good wetting property
- Provide mainly electrostatic stabilization.
.
Determining Dispersant Dosage Level
Like any other additive, more is not better. In fact, performance will decrease once past the ideal level. Once the dispersant is identified, a ladder study is best to determine the optimum level needed. The standard method is to measure mill base viscosity with increasing dispersant level and plot it. Figure below shows the determination of dosage level of a dispersant.
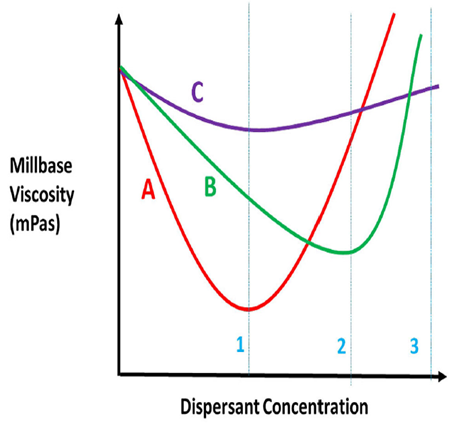
The key is not to formulate on a pinhead. We see that the red curve has the lowest viscosity and is the preferred dispersant, but its curve has a narrower plateau than the green or purple curves. At dispersant concentration 1, the red dispersant is the obvious choice. It uses less dispersant and has the lowest viscosity. But what if the concentration change between 1 and 3 is so small your production process cannot consistently weigh out the dispersant accurately within the range of the curve? Then the purple curve would be better. While the purple curve is the flattest of the three curves, in almost all areas the green curve has a lower viscosity and is preferred over the purple curve if the red dispersant cannot be used.
.
So why lower viscosity? As you increase the level of dispersant in the mill base, viscosity drops to the optimum level, then as you increase the dispersant level, dispersant/dispersant interactions will increase viscosity and make dispersion more difficult.
.
Important parameter while selecting a non-ionic dispersing agent is maintaining the correct Hydrophilic-Lipophilic Balance (HLB). HLB value ranges from 0 – 20, with 20 being completely water soluble. In aqueous systems the hydrophobic region attaches to the pigment and the hydrophilic region extends into the water phase. The opposite is true for solvent and 100%-solids based systems.
Often water sensitivity is a concern in coatings for either scrub or corrosion resistance. While this may lead you to consider a hydrophobic surfactant, you will need more of it, and it may not give optimum opacity, gloss, and tint strength. Often a hydrophobic surfactant will remain in the resin matrix, resulting in long-term water sensitivity, while a hydrophilic surfactant may leach out quickly giving better long-term water resistance.
.
Evaluating efficiency of Dispersing Agent
.
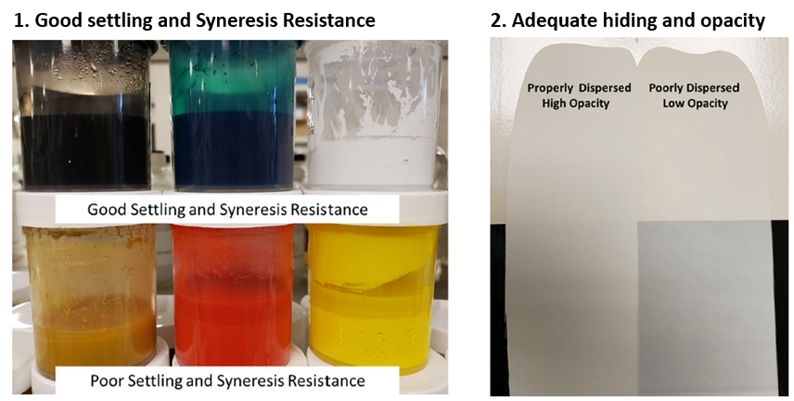
.
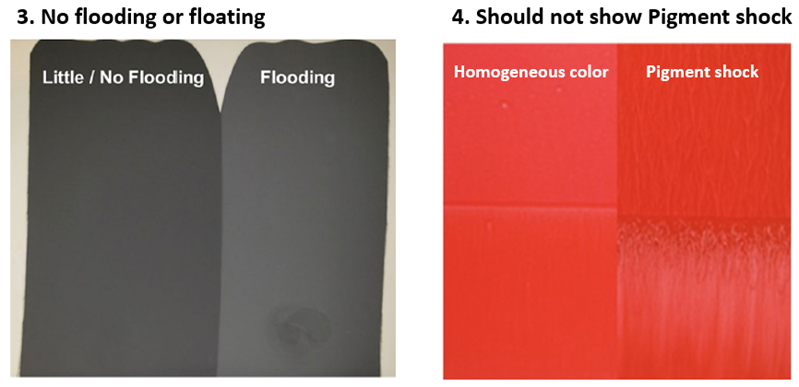
.
.
References
- How to select Dispersing Agents. Special Chem
- Introduction to Additives, Part 4: Dispersants. Mike Praw. Paints & Coatings Industry Magazine.