Film formation can be regarded by many as the most important phase/parameter/property when working with coatings and adhesives. Decades ago, when aqueous emulsion-based systems were being introduced as an alternate to solvent-based systems, they did not find much acceptance in the market because of their poorer film formation capabilities. However, over the years, lots of research has gone into improving the film formation ability of emulsions. The technology involved is quite interesting to know, hence we decided to discuss about it in detail here.
Film formation is the physical “solidification” of an emulsion paint. The film formation of polymeric emulsions can be divided into 3 steps:
- Concentration
- Compaction
- Coalescence
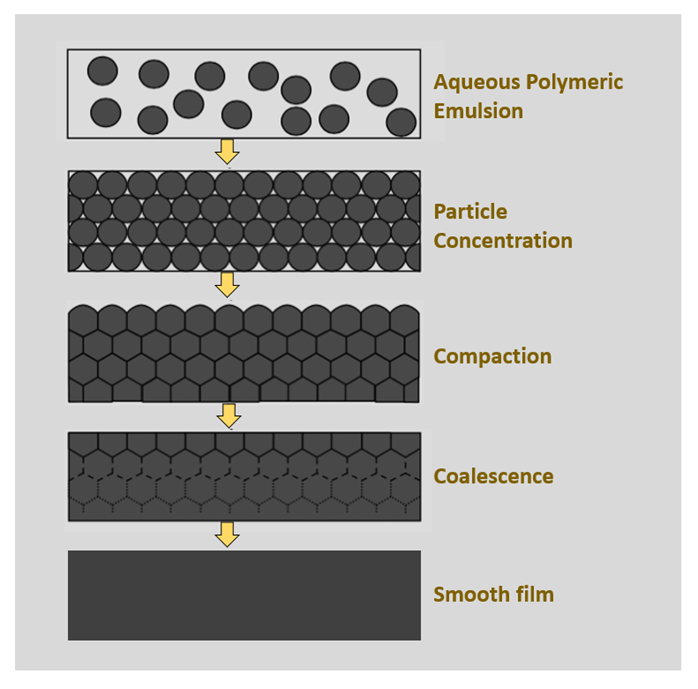
After the emulsion is applied on the surface, water evaporates, reducing the volume of the system. This reduction in volume causes the polymer particles to move closer to each other, increasing their concentration. As the water evaporates out completely, capillary force is generated in the system which causes the polymer particles to pack themselves in a compact form. In the final step of the film formation process, the particles arranged in the hexagonal structure coalesce together to form a smooth film.
But wait! Is coalescence so simple and straightforward?
No, we still must discuss two more concepts to completely understand film formation.
First is “Minimum film-forming temperature” (MFFT). MFFT as its name suggests is the temperature above which a given emulsion forms a smooth film. Below the MFFT, an emulsion paint forms a non-coherent, and mechanically unstable film. The MFFT depends on the structure of the polymer binder, its glass transition temperature, and on the nature and the amount of film-forming auxiliaries and other additives in the formulation.
MFFT and glass transition temperature (Tg) of the polymer are frequently confused with each other. Tg corresponds to the temperature at which the amorphous structure of the polymer begins to change from a glassy to a rubbery state. At temperatures below Tg, the polymer will be relatively brittle and unlikely to form a coherent film. Generally, one can consider MFFT to be about 100C higher than Tg for a given emulsion, but this is not the case always.
.
Second is “Film forming auxiliaries or coalescing agents”. Coalescing agents typically demonstrate one or more of the following effects, which aid in film formation:
- Lower the Tg of the polymer by easing deformation of particles
- Increase capillary forces by controlled evaporation of water
- Reduce repulsive forces between polymer particles
.
After film formation, conventional coalescent evaporates and allows the latex film to return to the initial Tg. Higher Tg latexes may yield harder, tougher films.
.
Another key property to is to check for hydrolytic stability of your coalescing agent. Coalescent that is pH sensitive may hydrolyze in architectural paints, which are commonly formulated to pH 9 or above. Esters like DB acetate are pH sensitive coalescent. When paints include alkali swellable thickeners, the pH drop could result in a decrease in viscosity. Paints with lower pH may also make the paint more susceptible to biological contamination.
Recommended dosage for coalescing agents varies from 4% to 12% based on emulsion solids. Hence always ask your emulsion supplier if the emulsion already contains any coalescing agents, to avoid adding excess in the formulation.
Having a uniform and smooth film helps in improving the overall coating properties such as less water absorption, scrub resistance, color strength and glossy appearance.
Coalescing agents can be broadly categorized into three groups:
- Hydrophobic coalescing agents
- Hydrophilic coalescing agents: water soluble
- Partially water-soluble coalescing agents
Table below summarizes the behavior, advantages, and disadvantages of these coalescing agents, to help the formulators in selecting the most appropriate coalescing agent in their formulation.
.
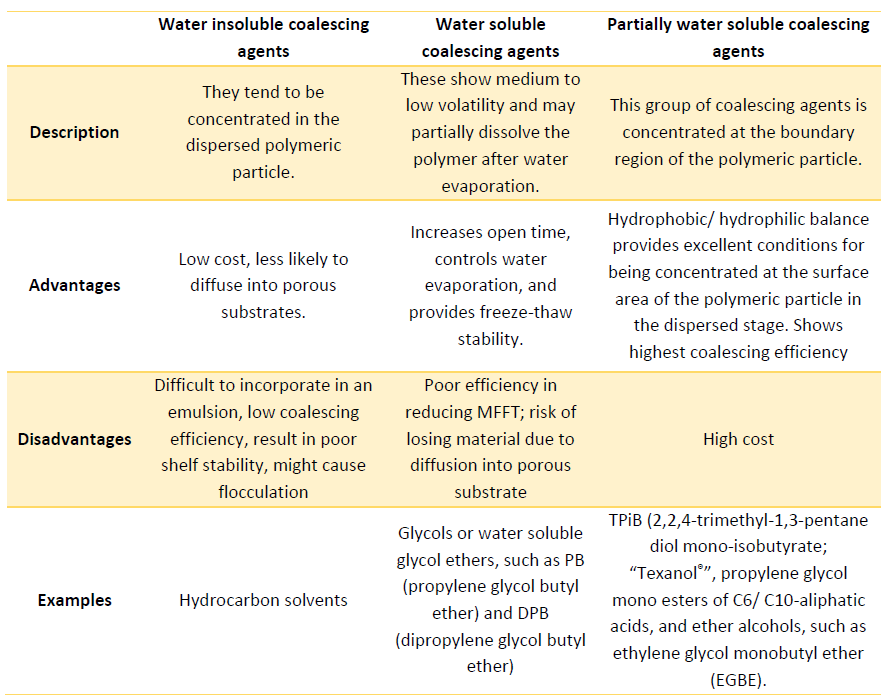
.
.
References
- BASF Insights. Developing a novel acrylic polymer for high performance in paint-and-primer-in-one exterior coating applications. Staff Writer. June 19, 2018.
- Influence of cosolvent retention on film formation and surface mechanical properties of water based acrylic coatings by atomic force microscopy. Progress in Organic Coatings. Qi Chen. January 2017.
- Drying, Film formation, and open time of aqueous polymeric dispersions. Imke Ludwig. 2008.
- European Coatings Tech Files. Film Formation. Peter Mischke. 2010