Waterborne Direct to Metal (DTM) coatings are increasingly important in the coatings industry due to their environmental benefits and performance characteristics. This article explores the key aspects of formulating these coatings, including trends impacting innovation, focus areas for technology development, advantages and disadvantages of waterborne DTM coatings, and formulation guidelines.
To perform its duty effectively, an anticorrosive coating must possess intrinsic durability, adhesion to the substrate, adequate flexibility, and toughness to withstand impacts and cracking as well as maintain its appearance when subjected to stress, swell, mechanical abuse, or weathering.
.
Metals protection by coatings is afforded by two main mechanisms in series: a barrier effect and an anti-corrosion action due to the presence of an active pigment. The barrier effect delays water entrance but, once water has reached the metal surface, the anticorrosion pigment action is the main protective effect.
.
Trends Impacting Waterborne Direct to Metal Coatings Innovation
The coatings market is seeing significant growth, driven by increased demand for sustainable and high-performance products. The total coatings market is valued at $1,619M, with the waterborne coatings market contributing $486M. Innovations in waterborne DTM coatings are crucial for meeting industry needs and regulatory standards. Despite the fact that waterborne systems still hold a relatively low share of the total market for anticorrosive coatings, the average growth rate for waterborne coating technology is larger than that for conventional solvent borne coatings.
.
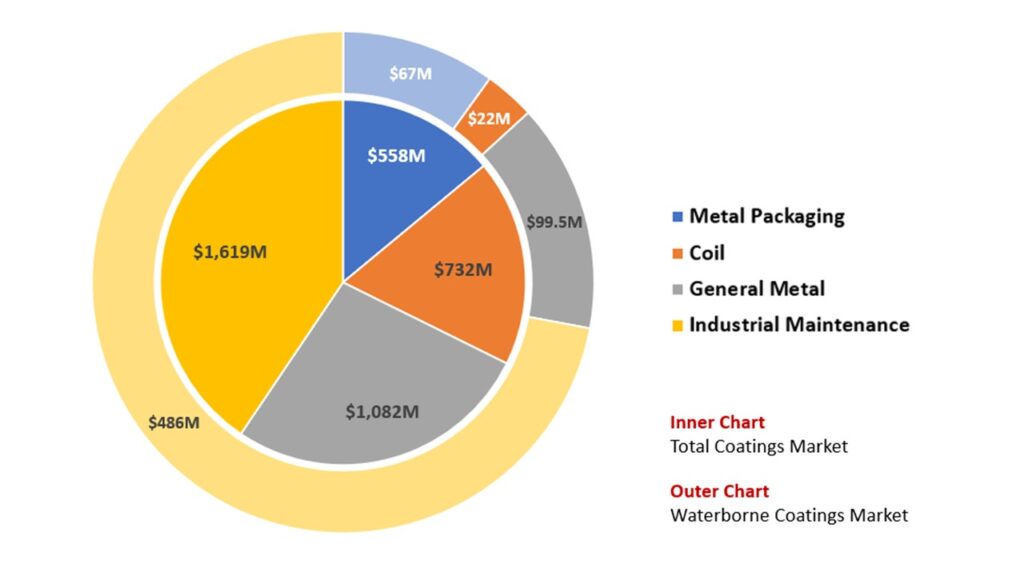
.
Focus Areas for Waterborne DTM Technologies
.
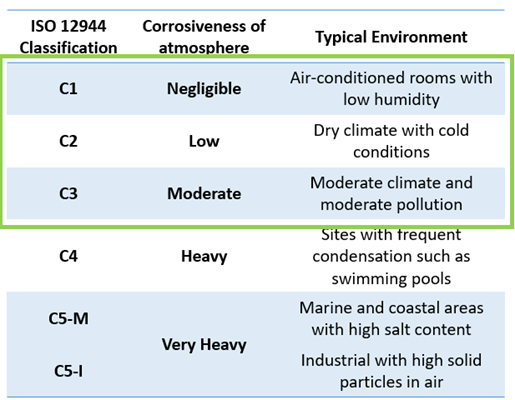
ISO 12944 classifies environments based on their corrosiveness, ranging from negligible (C1) to very heavy (C5-I). Understanding these classifications helps in designing coatings that can withstand specific environmental conditions.
Waterborne DTM coatings are typically used for application areas which fall under C1 – C3 category, e.g. building gates, road fences, balcony grills, home furniture, light duty industrial equipment etc.
.
Such categorizations will naturally be subject to debate because it is often difficult to specify corrosivity categories for one particular location (e.g., roads may be heavily salted during the winter in rural areas where the location can, in principle, be categorized as both C3 and C5). However, they do provide a useful frame of reference for typical conditions encountered by coatings during service.
.
.
Advantages & Disadvantages of Waterborne DTM Technologies
.
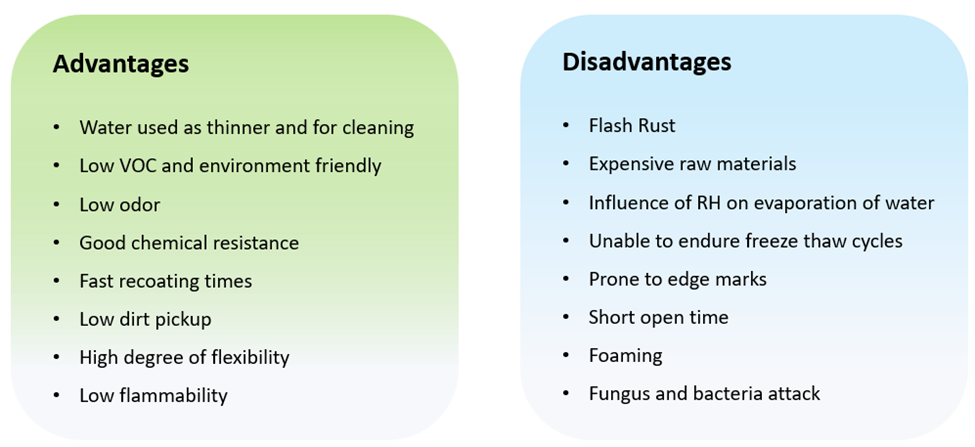
.
Formulating Waterborne DTM Coatings
Key Components for formulating waterborne DTM coatings:
1. Binder/Emulsion: Provides adhesion, water & alkali resistance. Typically, self-crosslinking with Tg>20°C.
2. Coalescent/Co-solvent: Improve film formation. Typically, a combination of hydrophilic (e.g. butyl glycol) and hydrophobic (e.g. DPnB) solvents are used.
3. Active Pigments/Anticorrosion Additives: These pigments are categorized by the way they work:
a. Active pigments (chemically/electrochemically) – e.g. Zinc phosphate, Zinc chromate
b. Barrier pigments (physically) – e.g. TiO2, mica, glass flakes, barytes
c. Sacrificial pigments (electrochemically/physically) – Zinc rich primers
4. Additives: Dispersing agents, rheology modifiers, biocides, UV stabilizers, defoamers, wetting agents, and adhesion promoters.
.
Selecting Fillers and Pigments
In coatings pigmented with spherical pigments, the aggressive species can migrate almost straight through the coating. When the coating is pigmented with lamellar pigments, the aggressive species are provided a tortuous path of diffusion.
.
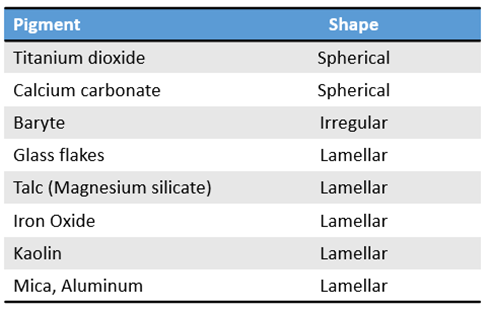
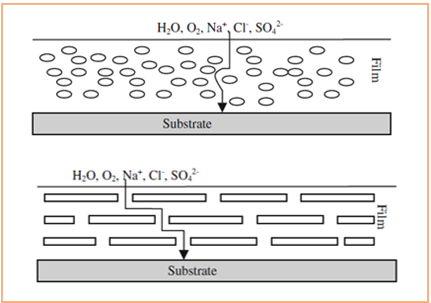
However, it must be noted that not all lamellar shaped pigments might be the right choice for the paint system. Kaolin, though lamellar in nature, is hydrophilic in nature, which will disrupt the water resistance property of the paint system. Glass flakes having higher particle size are only preferred for high build (thick) coating systems.
.
Selecting Active Pigments
In so-called zinc-rich coatings a high level of zinc dust is incorporated as a pigment. Particles of the less noble zinc in the paint film protect the ferrous substrate by acting as a sacrificial anode which corrodes in favor to the ferrous cathode. The sacrificial anode protects the ferrous cathode as long as zinc is able to pass into solution. Cathodic protection in this way is only possible if the zinc particles are in electrical contact with each other and the metal substrate. The basic requirement for sacrificial protection is for the sacrificial metal to be more electrochemically reactive than the metal substrate under the conditions of use.
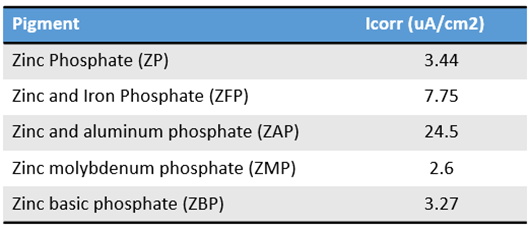
- Phosphates help in metal passivation by plugging pores and defects of the oxide layer on metal.
- Anticorrosive performance of pigments:
ZMP > ZBP > ZP > ZFP >>> ZAP - Corrosion reduction with ZMP was 25 times that of blank steel.
.
Selecting Defoamer
Unfortunately, there is no single defoamer for all systems. However, it is generally accepted that a defoamer should possess the following:
- Controlled incompatibility (insoluble in system)
- Low surface tension
- De-wetting characteristics
Broadly we can categorize the type of defoamer to be selected based on the coating chemistry as tabulated below:
.
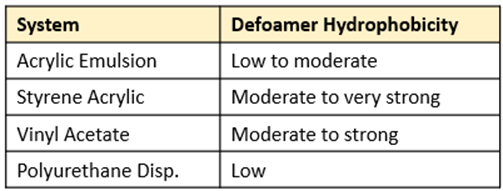
.
.
Selecting the base emulsion
Emulsion forms the body of the paint system and contributes to multiple performance properties. Hence one must ensure that the emulsion meets the following criteria:
- Have added anchorage sites for providing good adhesion to the metal surface.
- Have narrow particle size distribution to ensure continuous film formation, leaving no sites available for moisture penetration.
- Is hydrophobic and resistant to hydrolysis.
- Is nonconductive in nature when dried.
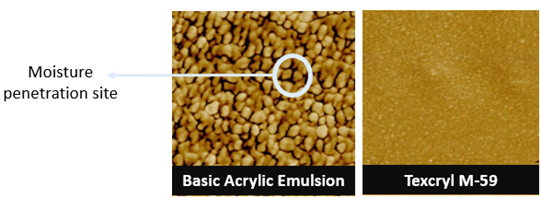
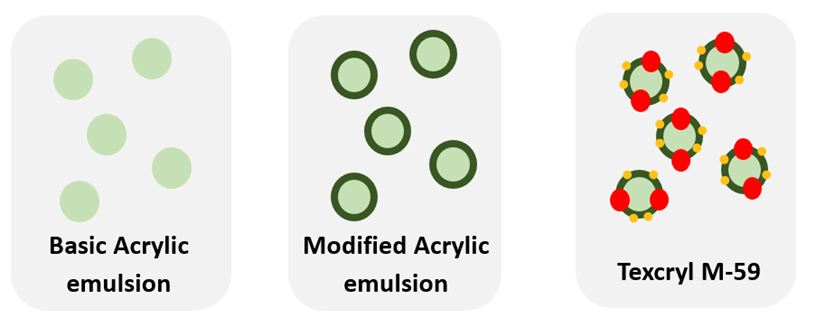
.
Performance parameters for Waterborne DTM Coatings
.
- Salt Spray Test (500 hours)
- Check for blistering in humidity test (45 days at 450C)
- Cross cut Adhesion
- 1 hour spot test for Chemical resistance (Caustic, gasoline, IPA, Ethanol, Muratic Acid, Brake fluid)
.
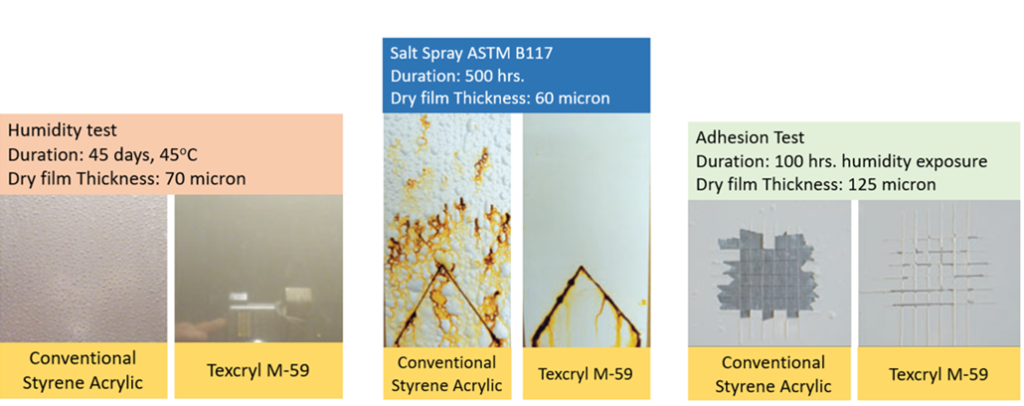
The images shown are for explanatory purposes only. Image reference: Asconium, Ascotec, France.
.
Guideline formulation (Red oxide Primer)
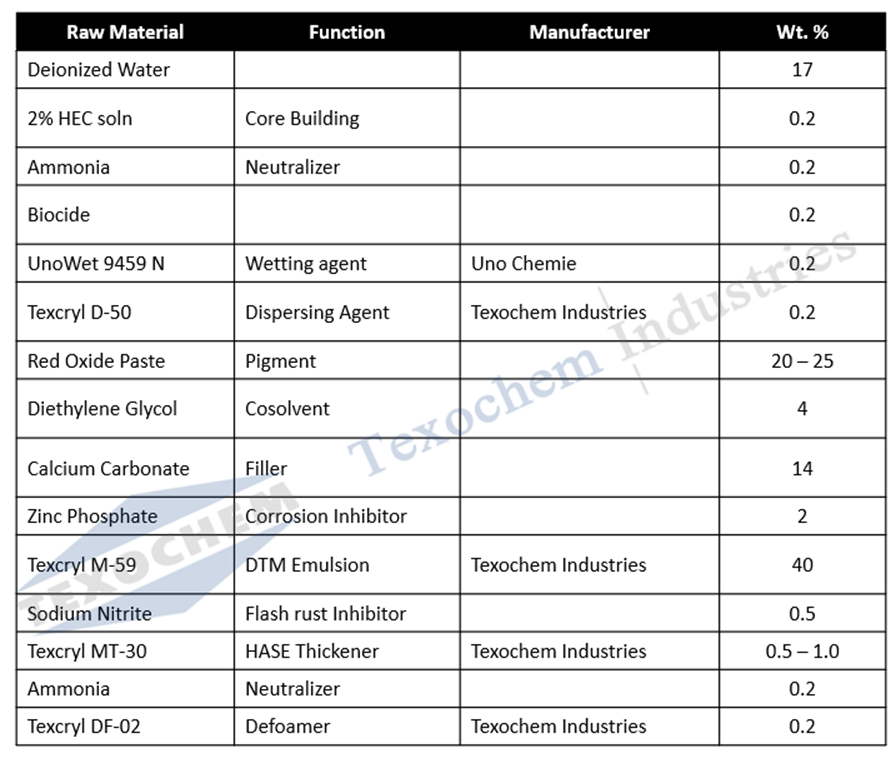
.
Conclusion
Waterborne DTM coatings offer a balance of environmental benefits and high performance. Understanding the formulation components, selecting appropriate pigments and additives, and addressing common defects are crucial for developing effective DTM coatings. Texochem Industries’ Texcryl M-59 emulsion demonstrates excellent performance across various tests, making it a reliable choice for waterborne DTM applications.