Extrusion based coating/laminating and adhesive based film laminating are different manufacturing techniques a converter can use to make a composite construction. The physical properties and performance characteristics of flexible packaging made by extrusion coating and laminating can be identical to that made by film laminating. Many of the major components of the final constructions are also the same. So which technique should be used for a particular product package? The decision is not an easy one, with equipment availability, run length, polymer specifications, and manufacturing efficiencies being some of the major variables in this equation.
.
Introduction
The performance properties of extruded and adhesive laminated structures are frequently dependent upon the types of polymers, adhesive, and surface treatment ingredients combined to deliver the intended package performance. Multiple performance criteria such as mechanical properties, gas and moisture barrier properties, seal ability, printability and cost will be integrated to satisfying the performance of both rigid and flexible packages.
Adhesive laminates can be made by dry bonding, wet bonding, UV/EB curing and by hot melt processes. Extrusion laminates are constructed by extruding a thin tie layer of a plastic material to bond together two dissimilar materials such as polymer film, paper, or foil. Furthermore, coextruded materials are produced by extruding several polymer layers simultaneously and then pressing/cooling them together. Incompatible layers are laminated together using a thermoplastic adhesive as a tie layer.
.
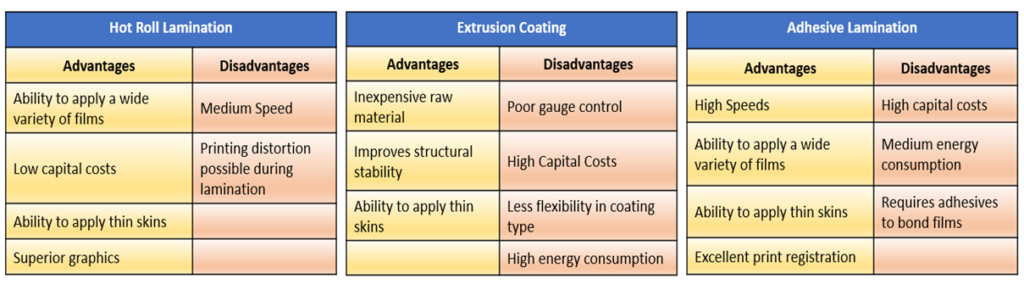
.
.
Adhesive Lamination: Wet & Dry Processes
Adhesive lamination is a preferred method of joining substrates when a film cannot be effectively processed through a coextrusion process because of equipment limitations (such as thermal damage by coextrusion). The manufacturing process of film laminates is a continuous process of coating the adhesive and bonding, with process differentiation defined by the type of adhesive used and how the adhesive is applied and converted. These processes are classified as either “wet” or “dry” lamination processes and are described in the tables below.
.
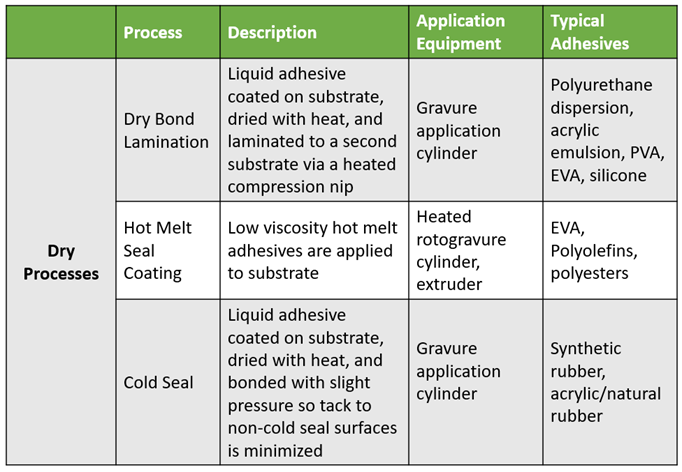
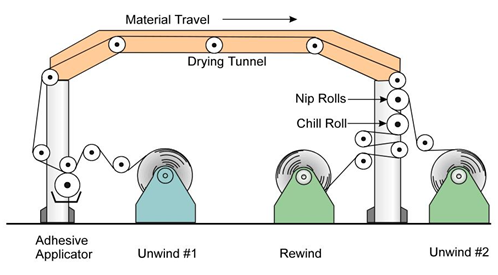
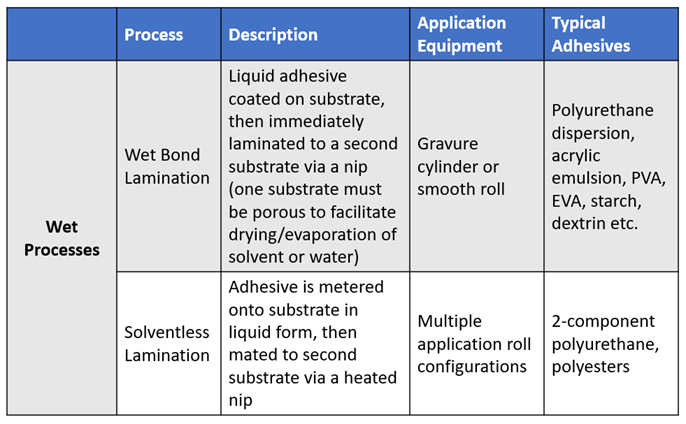
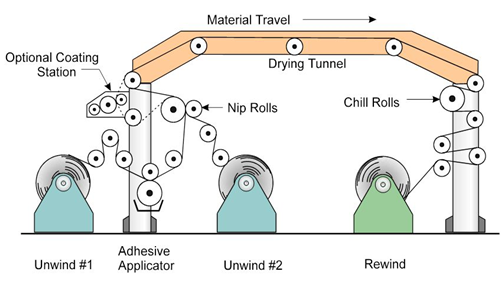
.
Hot Lamination Adhesives
Hot melt adhesives (HMA) in the laminating process span the base composition range of polyester, polyamide, EVA, polyethylene, and thermoplastic and reactive urethane. These adhesives are typically applied at ambient temperature to a substrate and activated using heat. A second web substrate is laminated to the first after the material is activated. HMA can also be applied directly and therefore more efficiently to the substrate via rotogravure, spray, or extrusion coating technology. Significant material savings can result by direct application of the hot melt adhesive, thus eliminating the cost associated with cryogenically created powders or formed films and webs. Also, ovens used to activate dry adhesives are not required in most cases, saving utility costs and floor space.
.
UV/EB Curable Laminating Adhesives
Ultraviolet (UV) or Electron Beam (EB) curing laminating adhesives are composed of acrylate/methacrylate monomers and oligomers. Aliphatic urethane acrylates are commonly used in laminations since they give good adhesion to most films, do not yellow, and have a very low application viscosity (350-450 cPs). In general, UV/EB laminating adhesives are directly coated on the surface of a film, nipped, and cured at line speeds which can be adjusted by substituting UV lamps of different intensity. The process is generally based on free radical curing of acrylates (For more details on UV and EB curing mechanism – please refer to the Texochem Tech File article: UV curing and EB curing technology).
.
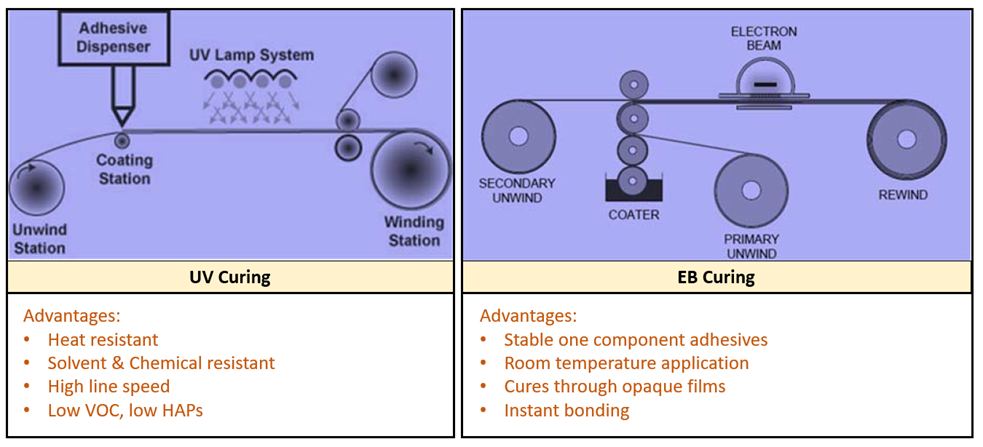
.
.
Extrusion Coating/Lamination
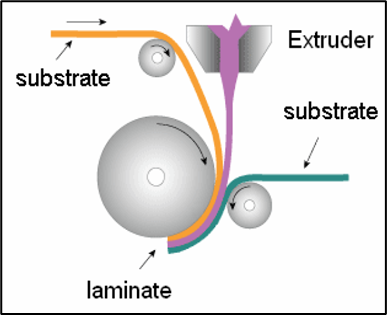
In extrusion coating and lamination, resin is melted and formed into thin hot film, which is coated onto a conveyed flat substrate such as paper, paperboard, metal foil, or plastic film. The coated substrate then passes between a set of counter rotating rolls, which press the coating onto the substrate to ensure complete contact and adhesion.
Extrusion laminating applies an extrusion coated layer which is used as an adhesive layer between two or more substrates. A second layer is applied to the extrusion coating while it is still hot and then pressed together by pressure rolls.
Examples of common composite films are the material for beverage pouch-stocks (combination of paper/PE/foil/PE) and composites for the medical packaging industry (polyester/PE/foil/PE). At the polyester-polyethylene(PE) and foil-PE interface; a primer, adhesive and/or a surface modifier is necessary so that the polyester will adhere properly to the PE. It should also be noted that when chemical primers are used to improve extrudate adhesion, it is typical that a corona treater is required to pretreat film prior to priming and subsequent extrusion.
.
Commonly used surface modification techniques to improve adhesion include corona, flame, ozone, and atmospheric plasma treatment.
.
Which Technique to use?
The selection of whether adhesive lamination or extrusion lamination methods are used depends to a large extent upon the equipment available with the converter.
Extrusion lines require extended runs to cost justify the time required for process variables to reach a steady state of operation, whereas adhesive lamination lines are conducive for small quantity runs.
If the converter has the opportunity to design and purchase a new line to use either extrusion or adhesive laminating processes, capital costs are a key consideration. The expenditures can actually be equal if considering a complex adhesive lamination line relative to a simple extrusion line. In this context of investment, the number of processes a converter requires can be a deciding factor.
Considering the performance of adhesive vs extrusion lamination, a key metric is barrier. When looking to achieve barrier properties by use of adhesive vs extrusion laminated inorganic barrier structures, the creation of oxygen barrier is dependent upon the lamination structures employed. As seen in the figure below, significant enhancements in oxygen barrier can be designed into a lamination process.
.
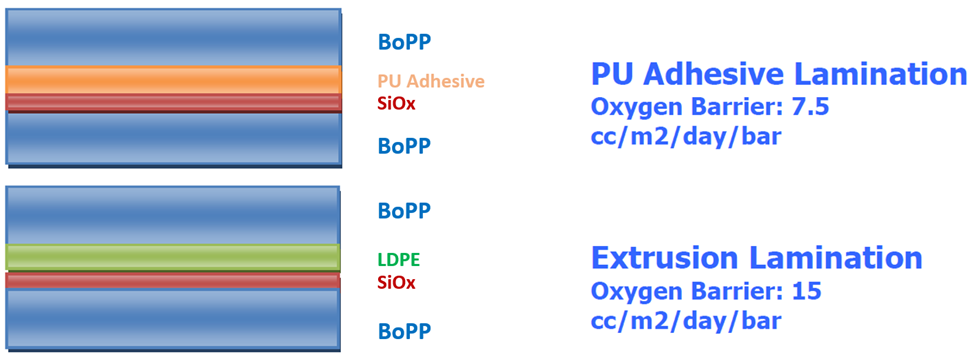
.
The choice of which process to employ is ultimately a complex one, but which may be best decided by the return on assets invested relative to the core competencies of the converter and the strategic market opportunities which will enhance this return.
.
References
- Enercon Industries Corporation. A Technology Decision. Rory Wolf.
- Adhesive and Sealant Industry. Manufacturing Pressure Sensitive Adhesive Products: A Coating and Laminating Process. Mausar J et al. 2005.
- TAPPI European PLACE Conference Proceedings. Transparent High Barrier Laminated Manufactured by Extrusion Lamination Process. Naegeli HR et al. 2007.
- TAPPI European PLACE Conference Proceedings. Adhesive Properties of Ethylene Acrylic Ester Maleic Anhydride Terpolymers in Extrusion Coating/Lamination. 2003.