One can commonly find blister packs in the consumer market today for packaging of toothbrush, medicines, batteries, chocolates, toys, stationaries, cosmetics etc.
Though the product inside the blister is the only important item for the consumer, they are typically unaware of the multiple processes and components which are required for completing the blister packaging. One of them is blister coating, which will be the main topic of study for this article.
Blister coatings fall under the category of packaging adhesives and can be simply defined as the coatings used for blister packs. Blister packs are of two basic types: In one variety the cavity is constructed of clear, thermoformed plastic, and the lid is formed of clear plastic or a combination of plastic, paper, and/or foil. The other type of package contains foil as an essential component of both webs, and its cavity is created by cold stretching. Figure below shows the basic configuration of a blister pack.
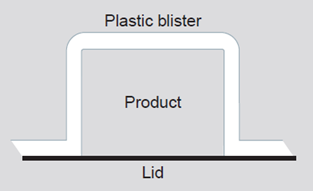
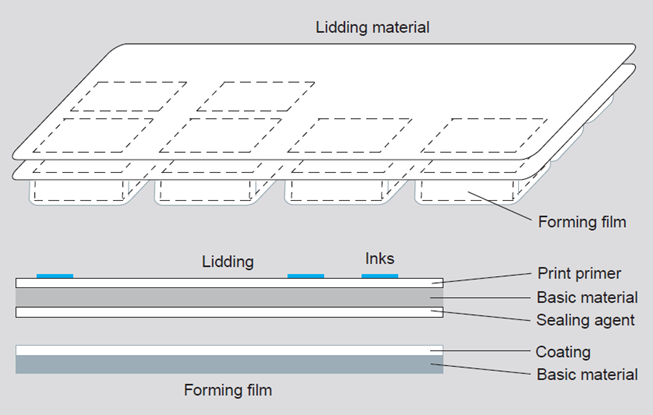
.
Blister coatings can be classified into
- Heat Seal Coatings
- Cold Seal Coatings
Heat Seal Coatings
For blister packages, heat-seal coatings are perhaps the most critical component in the entire system. The appearance and physical integrity of the package depends upon the quality of the heat-seal coating. Heat-seal coatings provide a bond between the plastic blister and the printed lidding material. These solvent- or water-based coatings can be applied to rolls or sheets of printed paperboard using roll coaters, gravure or flexographic methods, knives, silk-screening, or sprays. Whatever the system, it is essential that the proper coating weight be applied to the lidding material for optimum heat-sealing results.
A successful heat-seal coating for blister packages must exhibit good gloss, clarity, abrasion resistance, and hot tack and must seal to various blister films.
.
Hot tack is particularly important because the product usually is loaded into the blister and the lidding material heat sealed in place (face down) onto the blister. When the package is ejected from the heat-seal jig, the still-warm bond line must support its entire weight. A relatively low heat-seal temperature is desirable for rapid sealing and to prevent heat distortion of the blister film.
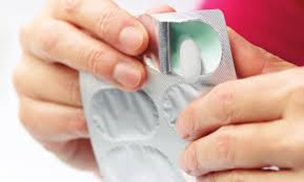
Although heat-seal coatings used for blister packaging still are predominantly solvent-based vinyl (because of their superior gloss), water-based products are making some inroads. However, they must be evaluated carefully for hot-tack properties, gloss retention, adhesion to specific inks, and seal ability to selected blister films. In addition, the heat-seal coating must precisely match the lidding material and the plastic material of the forming films. Precisely match means that with pre-determined sealing parameters, a permanent sealing effect between the lidding material and the forming film must be guaranteed under any climatic conditions. With the proper heat-seal coating, strong fiber-tearing bonds can be obtained. Specifically, the sealing strength must fall within predetermined tolerance limits and must be suitable for push-through or peel-off opening.
.
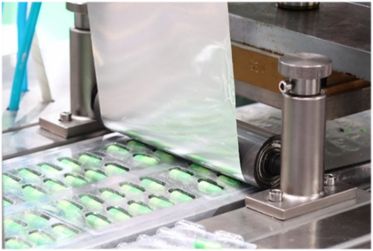
Tip to formulators:
- Keep your coating free from migratory chemicals to ensure bonding strength over time.
- A narrow glass transition temperature (Tg) must be achieved, along with a narrow polymeric dispersity index (PDI).
- Adding typical antiblocking additives will help in preventing blocking in stack of sheets but will reduce the sealing strength.
Common causes of blocking in heat seal coatings:
Blocking is the premature adhesion which causes the roll of coated material to form a log that cannot be unwound or separated.
The primary parameter to investigate in case of blocking is the coating thickness. Improper drying of the coating can also cause blocking.
When all volatile components, solvents are not removed from the coating, they act as plasticizer or softener in the coating film, causing blocking.
.
Excessive drying is equally bad and cause blocking too. High temperatures or longer heat cycles can cause any low molecular weight components in the coating to bloom to the surface, contributing to blocking. Another problem with excessive drying is that when the roll is wound, it retains heat and permeated through the entire roll. If too much heat is present, it will cause blocking over time.
Substrates can also play a vital role in causing the blocking issue. Few substrate materials contain low molecular weight components, or soft compounds, which migrate through the coating to the surface during the drying phase.
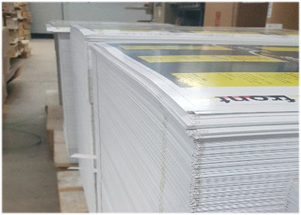
.
Cold Seal Coatings
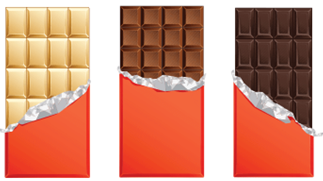
Cold seal coating/ adhesives are used in a wide range of applications including envelopes, chocolate wrappers, medical packaging for bandages, napkins, and specially where the object in the blister is heat sensitive, and heat seal coating process cannot be used.
The uniqueness of cold seal adhesives is that they seal only with themselves. When a substrate coated with cold seal coating meets another substrate coated with the same coating, the bond results by using simple pressure, involving no heat (hence the name “cold seal”).
Note: Cold seal adhesives from Pressure sensitive adhesives (PSAs), which are permanently tacky and must have a release paper to prevent them from sticking to anything until the final use.
.
Application Process: A film of cold seal adhesive is applied on each of the substrates that will bond together. The adhesive is then dried, which leaves a film with little to no tack, enabling it to be rewound or stacked in sheets without any blocking problems.
The strength of the bond with a cold seal coating will vary for many reasons, the most obvious being the adhesive formulation used. Adhesives can be formulated ranging from low strength to high strength. Another important parameter determining the bonding strength is the coating thickness.
The formulations for these products typically contain natural rubber latex, which is the predominant ingredient. Formulators also add tackifiers, plasticizers, extenders, or other ingredients. However, since rubber-based products are prone to yellowing and oxidation, an antioxidant is a must for such formulations.
Frequently encountered cold seal issues:
- Foaming
- Formation of lumps in the medium during application
- Quality variation due to seasonal fluctuations in rubber latex
- Lack of sealing strength
- Bad odor
- Blocking upon unwinding reels
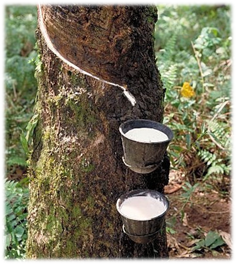
Recently cold seal coatings are being supplied in the aqueous form, made from vinyl copolymers. Main drivers for this are the elimination of natural rubber latex, suspected of causing allergy in sensitive individuals, and the reduction of the unpleasant organic smell. In the synthetic version, a reduced and different odor level was observed as well as excellent converting and sealing behavior.
Despite the advantages of the synthetic cold seal, which is a higher cost material, it has not been widely adopted. There have been successful developments such as minor modifications in the formulation to reduce smell (flash stripping of residual acrylic monomers, improved centrifuging of latex), more consistent natural latex (rubber from large plantations with cloned trees), to allow higher converting speeds (using surfactants) and changes necessary to comply with evolving legislation.
.
References
- Basic Configuration of Blister Packaging. Manuel Alejandro and Rodrigo Romero. Pharmaceutical Technology. 2000.
- Paper Film Foil Converter. PFFC Columnist PLC Probe. Common Causes of Blocking in Heat Seal Coatings. David Bentley. October 2000.
- PFFC Columnist PLC Probe. About Cold Seal Adhesives. David Bentley. January 2006.
- Paper and Paperboard Packaging Technology. Blackwell Publishing. Edited by Mark Kirwan. 2005.