Surface tension is involved in almost every way in coatings technology. There is no denial in saying that surface tension is amongst the key decisive factors for the longevity and qualityof the applied coatings. Defect-free appearance & color, corrosion behavior, electrical conductivity, wetting behavior, adhesion of coatings and many other properties are determined by surface properties of the system involved.
To understand surface tension, it is important to understand its cause.
Cohesive force is the force of attraction between the similar molecules. Let’s refer to the two molecules A & B in the figure below. Molecule A is surrounded by similar molecules, and hence the net attractive force acting on molecule A becomes zero. Whereas in case of molecule B, net attractive force is acting in the downward direction. So, we can say that cohesive force acting on molecule B is greater than that acting on molecule A. Hence surface tension of molecule B is higher than A.
When a liquid coating is applied on the surface, surface tension forcescome into play to redistribute the coating layer.
If the surface tension of a liquid coating is higher than that of the substrate the coating, the coating will obtain the lowest possible common surface with the substrate. Thus, the coating will not wet the surface properly leading to surface defects.
.
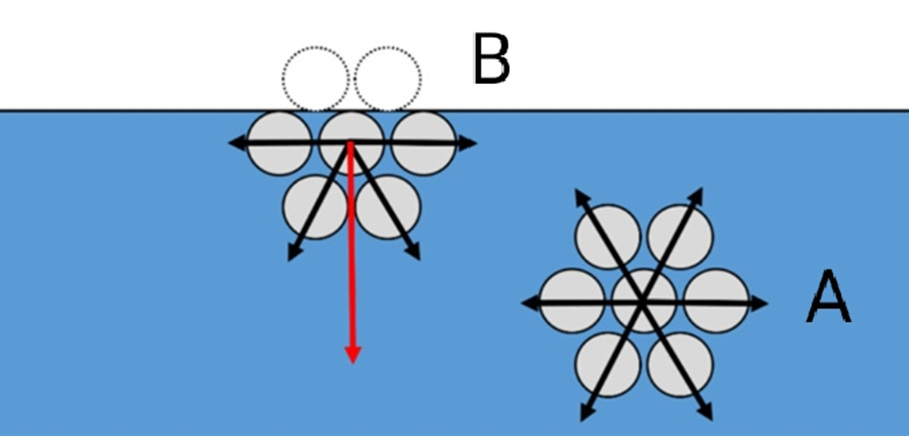
.
.
Why is Contact angle an important parameter?
Contact angle (θ) is the angle which the liquid drop forms with the surface in contact. It is an indication for the ability of the liquid to spread on the surface, respectively a possibility to determine the dimension for the surface tension relative to a reference.
If θ = 0⁰ then wetting takes place easily
If 0⁰ < θ > 90⁰, partial wetting occurs
If θ > 90⁰ then wetting is difficult
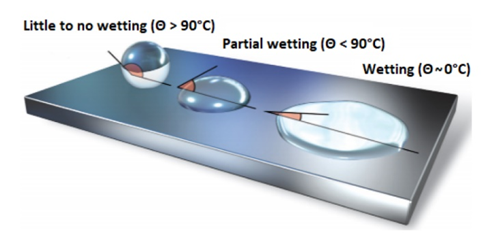
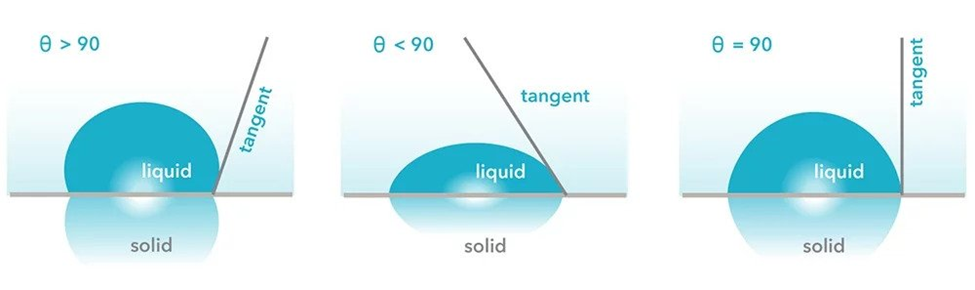
.
Therefore, substrate wetting depends primarily on the surface tension of the paint and on the surface tension of the substrate to be coated. To allow for proper wetting and adhesion between the layers, the surface tension of the coating must be lower than the substrate. By comparison:
Solvent borne systems have naturally low surface tensions and can easily wet most substrates. Water-based systems often have high surface tension resulting in poor wetting and require use of suitable raw materials or substrate treatment for effective substrate wetting.
.
Coating properties affected by surface tension
Leveling: Defects like cratering, fisheyes and pinholes are commonly caused by impurities like dust and small particles which have low surface tension, making it difficult for the coating to form a uniform film. Proper levelling can be achieved by lowering the surface tension of the coating system, to ensure complete wetting of the substrate.
Foaming: Foaming is entrapped air in liquid which can cause defects like pinhole and fisheye. The air dispersion (bubble) in liquid is stable because of presence of small particles in the medium which reduces surface tension. Anti-foaming agents are commonly used to avoid this defect as they reduce the stability of air dispersion.
.
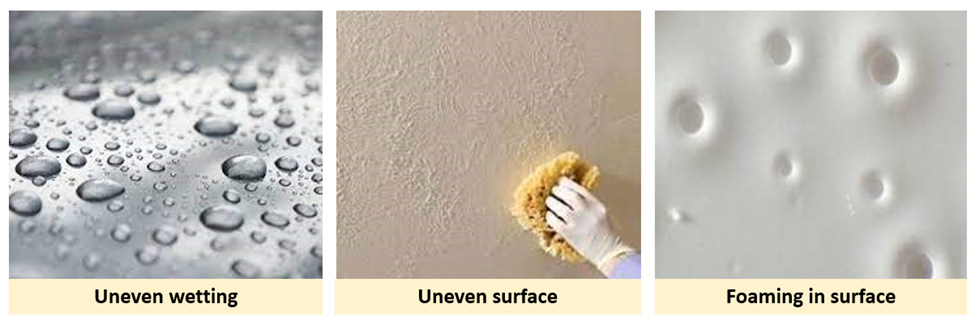
.
.
Importance of Surfactants
Surfactants are the additives used in coating formulation to achieve the desired surface tension in the system. There are variety of surfactants, each having its own performance features and benefits. However, they are often classified according to the composition of their “head” into four primary groups: anionic, cationic, non-ionic, and zwitterionic (dual charge)
Anionic surfactants are sulfonate, carboxylate, and phosphate ester.
Cationic surfactants are typically amine derivatives, such as quaternary ammonium compounds.
Non-ionic surfactants classes majorly include are polyglycol ether derivatives, such as alkyl- and alkyl-aryl polyethylene glycol ether (alkyl PEG), polypropylene glycol ether and block copolymers of polyethylene glycol and polypropylene glycol.
Zwitterionic (amphoteric) surfactants include betaines, amine oxides
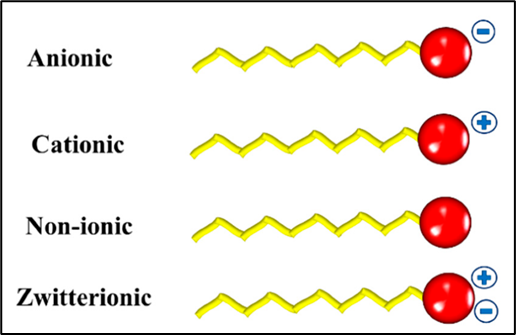
.
.
References
- Special Chem. Surface Tension: A Property to Determine Coating’s Effectiveness.