In the early days, emulsion polymerization technique was explored in the effort for producing synthetic rubber latexes (e.g., Styrene butadiene rubber), but the versatility of emulsion polymerization was quickly recognized and led to an extremely wide range of polymers being produced in this way, including synthetic elastomers, bulk plastics, and polymer latexes for use in variety of coating applications.
Emulsion polymerization is one of the types of free radical polymerization techniques ( the other common ones being bulk, solution and suspension polymerization). But amongst all emulsion polymerization has attracted most interest in industrial and academic setting because of the advantages it provides over other types of polymerization techniques:
- Fast dissipation of heat during polymerization
- Forms high molecular weight polymers at lower viscosity
- Ability to control submicron particle size and morphology
- Polymers can be used directly
- Can be used for tacky polymers
Emulsion polymerization usually produces latexes with spherical particles, which have a higher packing factor, hence do not show high viscosity as a different latex would show at equal concentration.
Before discussing the mechanism and intricacies of emulsion polymerization, it is important to study the key raw materials required for this process:
.
Monomers:
Main requirement is that the monomers can undergo free radical chain polymerization and they do not react with water. Monomers with limited solubility in water (neither very high nor very low) are most useful. Major classes of latexes used on coatings are based on acrylic, methacrylic esters, and on vinyl esters.
Methacrylic acid and acrylic acid improve colloidal stability, affect flow properties, improve adhesion, and give carboxylic acid groups to serve as cross linking sites.
Hydroxyethyl acrylate and hydroxyethyl methacrylate provide hydroxyl groups for crosslinking.
.
Initiators
Initiators selected should be such that they are soluble in water. Most preferred initiators are persulfate (SO52- or S2O82-) salts (ammonium persulfate/ potassium persulfate)
For polymerization at lower temp, addition of reducing agents accelerate radical production. Common reducing agents include mixture of ferrous, thiosulfate (S2O32-), and persulfate salts. Processes using this type of initiation are called redox emulsion polymerization.
It is common to add more lipophilic “chaser” initiator in the late stages of the semicontinuous process to facilitate conversion of monomer to high levels (>99%). E.g., t-butyl hydroperoxide.
.
Surfactants:
Both anionic (sodium lauryl sulfate – SLS) and nonionic (NP ethoxylates) surfactants are used. Typically, concentration of anionic surfactants varies from 0.5-2.0% of monomer concentration; and concentration of nonionic surfactants varies from 2.0-6.0% of monomer concentration.
Surfactants help in stabilizing the hydrophobic monomer particles, forming micelles in the water phase and promotes particle nucleation for polymerization.
Anionic surfactants lead to formation of rigid particles resulting in latexes which have low viscosity at high solids. Whereas nonionic surfactants lead to lower polymer solids at high viscosity.
At the same surfactant concentration, a surfactant with lower CMC will give smaller particle size. Particle size is much broader when anionic surfactants are used and approaches a monodisperse particle size when nonionic surfactants are used.
.
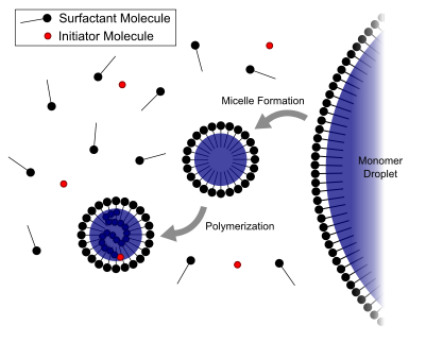
Figure 1: Schematic diagram of emulsion polymerization
.
Process mechanism
Emulsion polymerization mechanism can be divided into 3 intervals.
Interval 1: Waterborne free radicals first polymerize with monomer molecules dissolved in the continuous aqueous phase. This results in the increased hydrophobicity of oligomeric radicals. When a critical chain length is achieved, these oligomeric radicals become so hydrophobic that they show a strong tendency to enter the monomer-swollen micelles and then continue to propagate by reacting with those monomer molecules therein. Consequently, monomer-swollen micelles are successfully transformed into particle nuclei.
Hence increase in particle number and occurrence of particle nucleation is observed in
Interval 1. These embryo particles continue to grow by acquiring the reactant species from monomer droplets and monomer-swollen micelles, exhausting most of the surfactants by the end of this phase.
Interval 2: Polymerization continues, and polymer particles increase in size until monomer droplets get exhausted. Monomer droplets act as reservoirs to supply the growing particles with monomer and surfactant species.
Interval 3: The polymer size increases as latex particles become monomer-starved and the concentration of monomer in the reaction loci continues to decrease toward the end of polymerization.
Particle size is larger when the turbulence and agitation intensity is high.
.
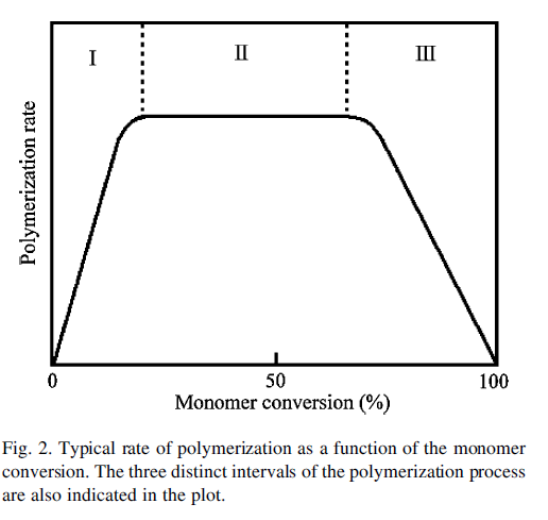
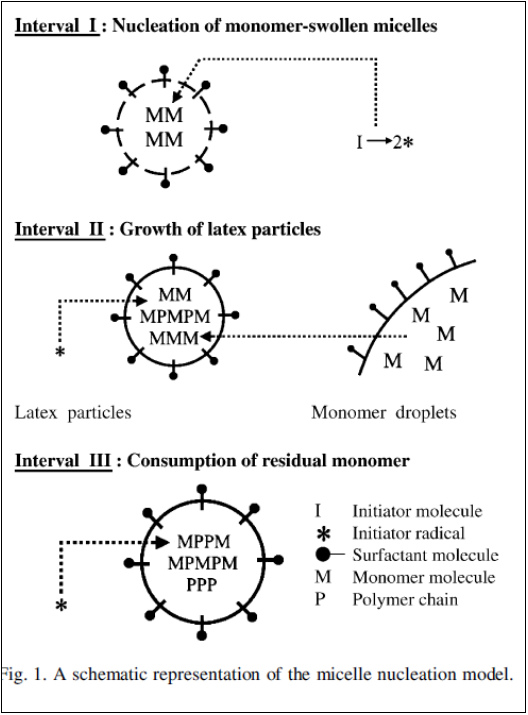
Figure 2: Intervals in emulsion polymerization
.
Typical emulsion polymerization formulation
Ingredients | Styrene butadiene copolymer | Polyacrylate emulsion |
---|---|---|
Water | 190 | 133 |
Butadiene | 70 | – |
Styrene | 30 | – |
Ethyl acrylate | – | 93 |
2-chloroethyl vinyl ether | – | 5 |
p-divinylbenzene | – | 2 |
Sodium lauryl sulfate | 5 | 3 |
Potassium persulfate | 0.3 | 1 |
n-Dodecyl mercaptan | 0.5 | – |
Sodium pyrophosphate | – | 0.7 |
Conditions | ||
Time | 12 hrs | 8 hrs |
Temperature | 50oC | 50oC |
Yield | 65% | >98% |
.
References
- Biomacromolecules. Fundamentals of Emulsion Polymerization. Peter Lovell. 2020-2021.
- Intech Open Book Series. Emulsion Polymerization Mechanism. Abdelaziz Nasr Moawed Bakr El-hoshoudy. January 2018.
- Progress in Polymer Science. Emulsion polymerization mechanisms and kinetics. C.S. Chern. April 2006.
- Organic Coatings – Science and Technology. 3rd Edition. Wiley 2007.