Need for replacing Polyethylene (PE)
The aim is to reduce the use of petroleum-based plastics. To enhance moisture resistance and grease resistance, paper-based packaging is frequently coated with polyethylene (PE). However, packages coated with PE may be challenging to recycle at a standard recycling facility. Often PE coatings may contaminate fibers during the repulping process, prohibiting the fiber from being recycled. The vast majority of polyethylene coated substrate is dumped into landfills where the paper portion degrades quickly, while the PE portion is estimated to take decades to breakdown. Polyethylene has dominated as a barrier coating in packaging applications because of its low cost, versatile properties, and the ease with which it processes.
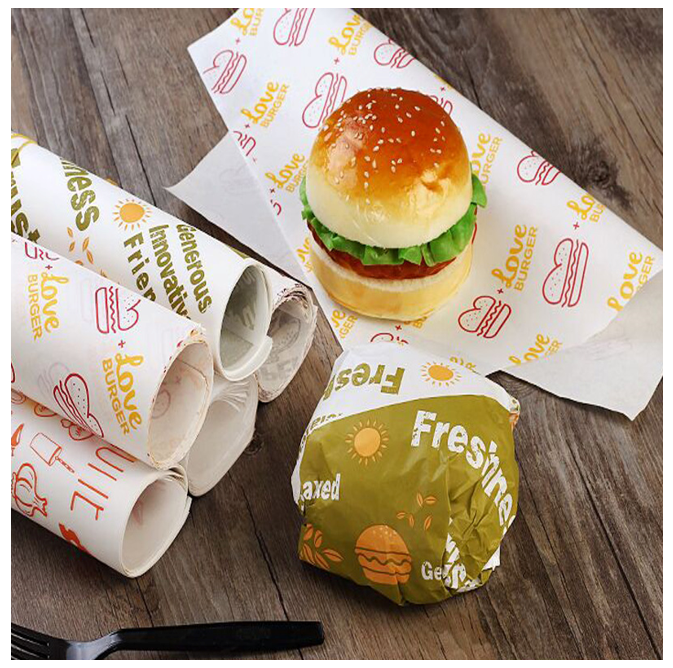
PE coated paperboard and paper are considered to be “bullet proof” by many, offering an exceptional barrier performance. Therefore, these substrates are broadly accepted and are generally not subjected to barrier testing by printers or converters.
However, now more and more printers and converters are responding to requests for paper and paperboard coatings that can replace petroleum-based extrusion coated polyethylene. Alternative barrier coating products that are safe for the environment are in favor due to brand marketers, legislative, political and consumer pressure.
.
What are barrier coatings?
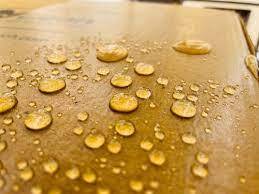
Water based barrier coatings are water-based dispersions of film forming polymer(s), additives, and possibly pigments. Barrier coatings seal the substrate surface and protect the packaging from external and internal influences. The packaging remains attractive and can fulfil its functionality without restrictions. Depending on the product, barrier coatings offer adequate protection against fat, water, water vapor, dairy products, alcohol, oil, or alkali for the packaging. Due to their versatility, they are used for a wide range of applications.
Applications for barrier coatings include food bags and wraps, food trays, paper plates and cups, take out containers, folding cartons and boxes, flexible packaging, and other protective packaging. Food packaging & food service products can rapidly lose their appeal to consumers if grease and oil staining, or water degrade their appearance.
Barrier coatings are highly specialized systems. Mostly, the barrier effect depends on the filling material, the substrate used and the application weight. To be able to make the right recommendation, information on the printing process, substrate, finishing, and final packaging is necessary.
.
Desired barrier coating properties
Depending on the product, barrier coatings are required to show certain valuable characteristics. Compiling the different important properties encompassed by barrier coatings:
- Oil & Grease Resistant
- Liquid Water Resistant
- Low in Odor Permeability
- Visual appearance (glossy, satin, matt)
- Heat seal ability
- Non-blocking
- High wet block resistance
- High scuff resistance
- Heat resistant
- Recyclability
- Consistent Coefficient of friction (COF)
- Direct food contact FDA compliant
Heat Sealable Barrier Coatings
Many paper or paperboard packages, for example, paper cups for food or drink services require the paper or paperboard be heat sealable, making it possible to form cups on a cup machine. Polyethylene (PE) extrusion coated paperboard currently still dominate in such applications by providing both required barrier and heat seal properties. However, as discussed above there are increasing demands for replacing PE with a barrier coating which not only provides excellent water and oil resistance, but also can seal the paper material on application of heat.
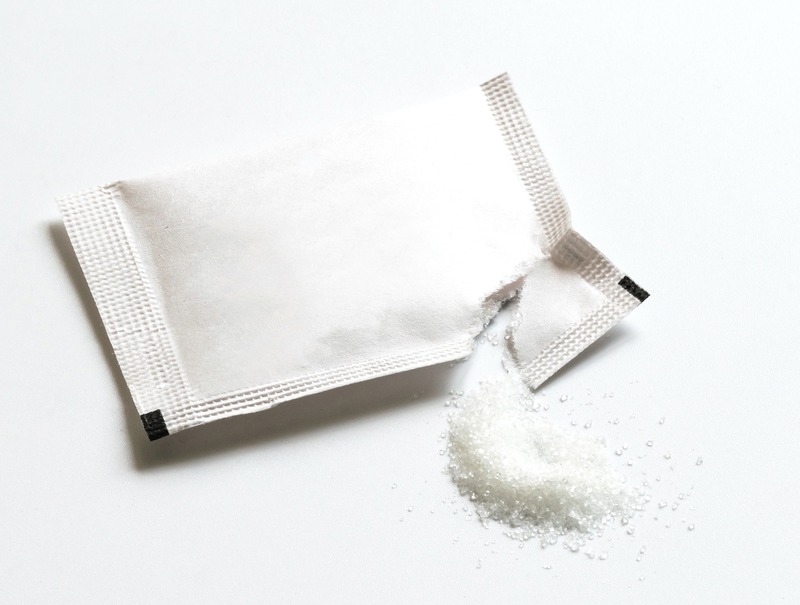
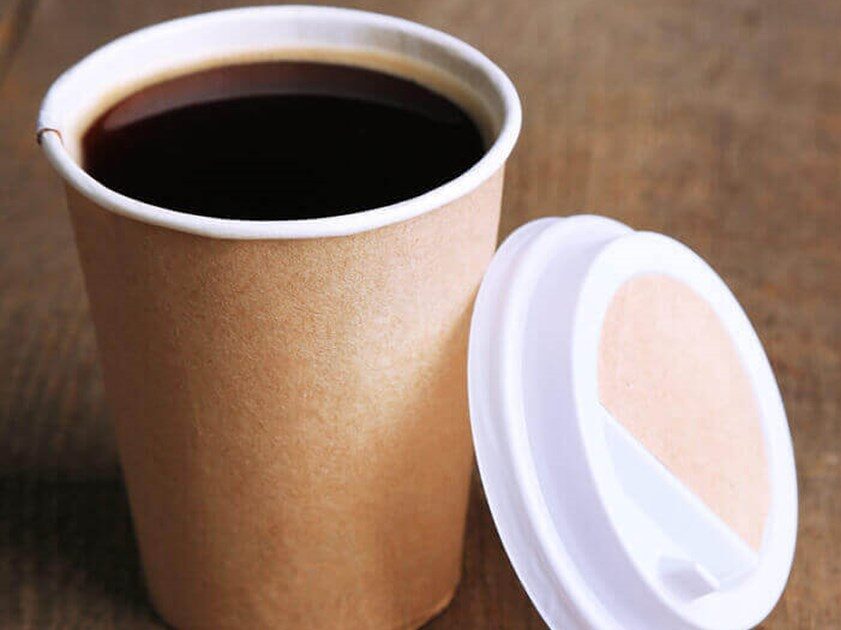
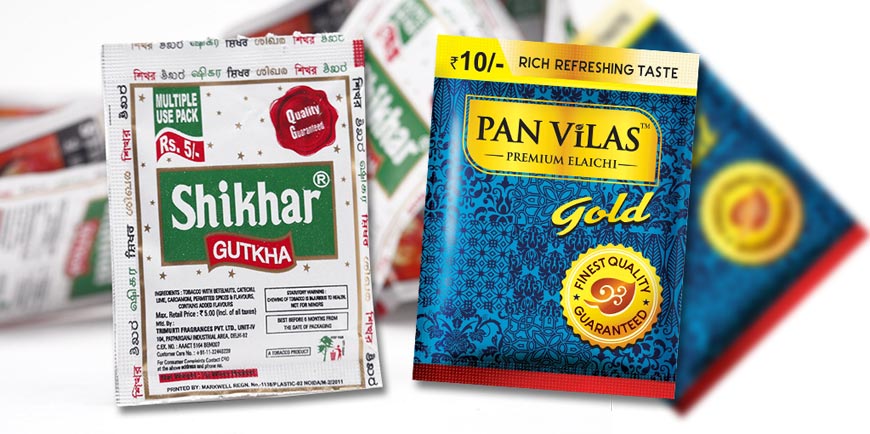
Most polymers in aqueous coatings are amorphous and do not have a melting point as PE (110°C). Therefore, binders or polymers in aqueous coatings often gradually soften or become sticky at elevated temperature (49-54°C) and/or pressure in production, storage, shipping, or converting process of aqueous coated paperboard, causing blocking issue of the coated paperboard, which usually does not occur with PE coated paperboard in practical applications.
This blocking issue becomes even more critical for aqueous barrier coated paperboard that requires high barrier properties and needs to be able to heat seal in converting packages such as cups and aluminum pouch packaging. Hence maintaining the glass transition temperature of the binder for such applications becomes a very critical parameter.
.
Testing barrier coating properties
.
Cobb Test
The Cobb test determines the amount of water absorbed into the surface by a sized (non-bibulous) paper, paperboard, and corrugated fiberboard paper or paperboard sample in a set period, usually 60 or 180 seconds (Cobb60 or Cobb180). The water absorption is expressed in g/m².
.
Kit Test
Kit test is typically performed to evaluate the oil and grease resistance (OGR) properties of the barrier coating. 16 test solutions are prepared by varying the concentrations of Castor oil, Toluene and Heptane. Substrate coated with the barrier coatings are then tested for their resistance to these solutions. Higher the Kit rating, higher is the OGR properties.
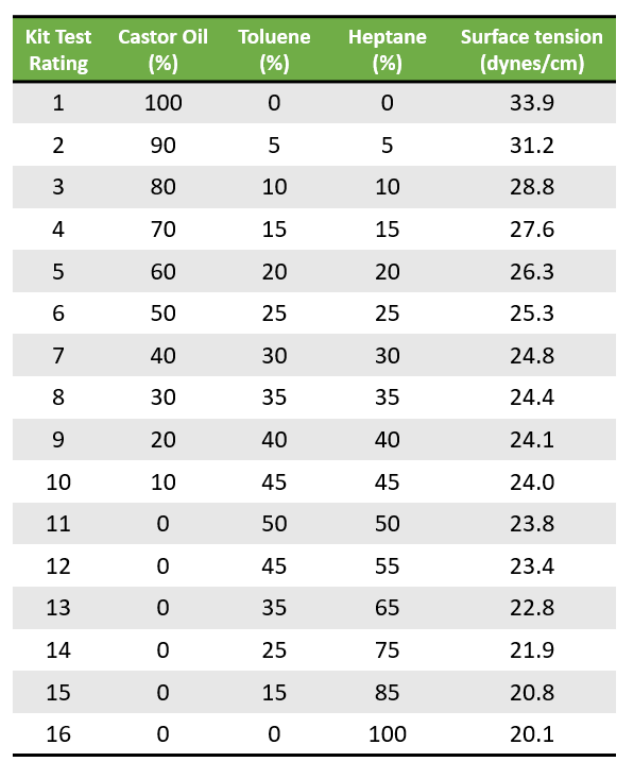
References
- Actega. Water based Barrier Coatings
- Cork Tech Talk Blog. Poly (PE) Replacement Barrier Coatings and Test Methods. Elmer W Griese Jr.
- HB Fuller. Water-based Barrier Coatings.
- Heat Sealable Barrier Paperboard. Patent WO2018156685A1.
- Paper and Paperboard Packaging Technology. Blackwell Publishing. Edited by Mark Kirwan. 2005.